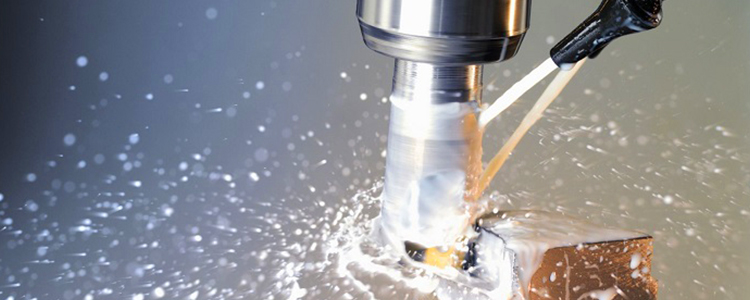
Recycling coolant using this simple method is highly economical and easy to implement. Successful recycling can significantly reduce the costs associated with using coolant/metalworking fluids. This program is one of Eonchemicals’ technical services designed to ensure customer satisfaction.
The disc brake industry is one of the automotive sectors that uses grinding coolant in the surface grinding process. The resulting grinding residue (chips) is fine and gradually accumulates into sludge, which is then channeled into a holding tank. Since chips interact with the coolant, the coolant is carried along with the chips into the sludge tank (carry-off). The more sludge that is collected and disposed of, the more coolant is wasted (inefficient).
Solution
To address this issue, Eonchemicals has implemented several steps:
1. Coolant Feasibility Analysis
Based on laboratory analysis, it was concluded that the coolant, commonly referred to as metal coolant, in the sludge tank is still usable.
2. Sludge Tank Modification
After modifying the sludge tank by adding a filter, the coolant can be better separated from the sludge.
3. Filtration
The coolant that has been separated in the modified sludge tank is then filtered in a filtering drum to obtain ready-to-use coolant. After passing through this filter, the coolant can be reused for the grinding process.
Recycling Results
With the successful implementation of the recycling program, customers achieve cost savings on coolant usage by reducing the amount of coolant discarded with the sludge. In addition to the coolant recycling program, a tramp oil terminator is needed to address contamination issues.
If you would like assistance with a recycling program as described above, please contact us.
Consult with EON Now
We are ready to listen and provide the right chemical solution for you. Consultation with our experts is free!
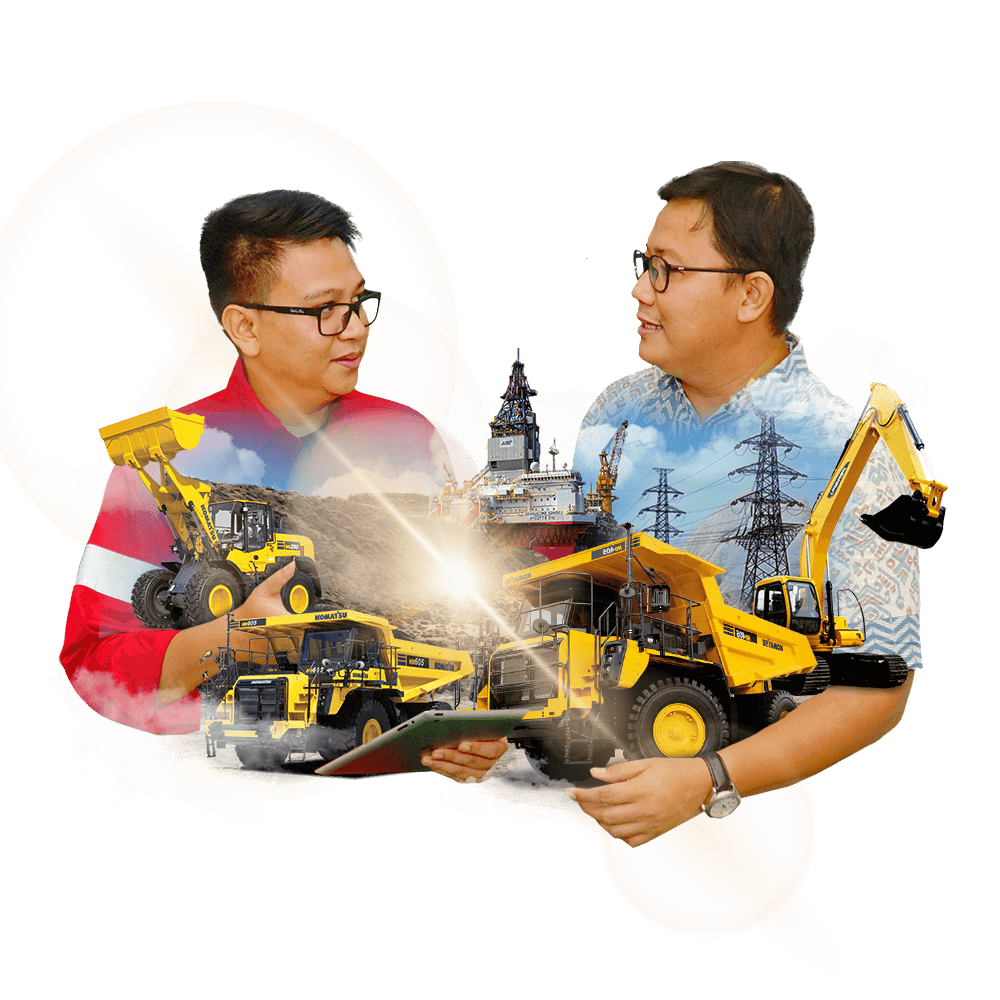