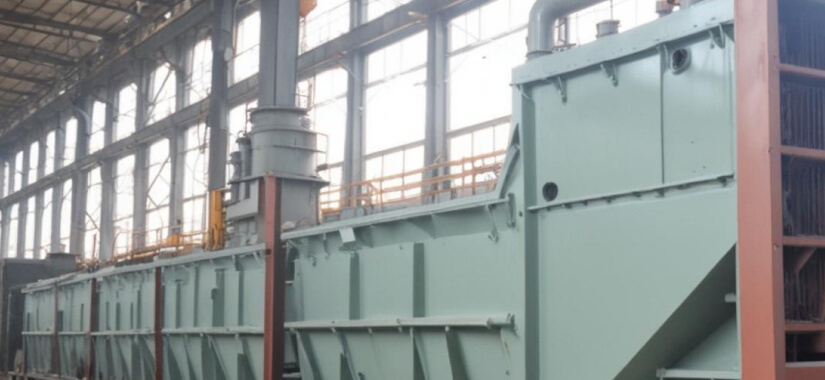
The quenching process in the cement industry is a critical stage in manufacturing that involves rapid cooling of freshly heated clinker from the kiln to produce cement.
After clinker is formed in the kiln at high temperatures, the quenching process is carried out to prevent the clinker from turning into crystals. This rapid cooling is performed using air or water in the quenching chamber to maintain the desired crystal structure of the newly formed clinker.
Several problems and effective solutions from Eonchemicals include:
1. Problem: High-Temperature Grease
The issue of high-temperature grease in the quenching process within the cement industry includes challenges in maintaining optimal performance and longevity of lubricants used on machine components exposed to high temperatures.
High temperatures can cause grease degradation, reduce viscosity (making it thinner), and decrease lubrication efficiency. This can lead to increased friction and wear on machine components such as bearings and gears, potentially causing mechanical damage.
Solution: Molykote / Dow / LE
Molykote, Dow, and Lubrication Engineers (LE) are effective solutions for high-temperature grease issues as they are specialty greases designed to handle high temperatures optimally. These products contain additives such as molybdenum disulfide (MoS2) or other additives that enhance the grease’s resistance to extreme temperatures, maintaining viscosity, and lubrication stability during intensive operations.
Eonchemicals is the official distributor in Indonesia for these products. Through an official distributor, you will be assured of the product’s authenticity and quality.
Please chat with us on WhatsApp for a free consultation on high-temperature lubrication programs.
2. Problem: Motor Cleaner for Gear Box
The issue of motor cleaner for the gearbox involves maintaining cleanliness and optimal performance of the equipment. Dust and fine particles from raw materials can accumulate around the gearbox, disrupting internal functions such as bearings and gears.
This problem can certainly lead to increased friction, wear, and even mechanical damage if not properly addressed.
Solution: EonMotor 100
EonMotor 100 is a chemical cleaning liquid designed to clean electric motors and dynamos from oil and grease contaminants. This product is highly effective in removing contaminants.
This cleaning liquid helps keep the electric motor clean and functioning properly. This condition is essential to extend the motor’s lifespan and ensure more optimal performance.
3. Problem Quenching Process: Road Dust
The issue of road dust in the quenching process area within the cement industry involves controlling the dust generated in that area. Dispersed dust can cause various problems, including visibility issues, health concerns, and equipment damage.
Poorly controlled dust can spread to the surrounding environment, polluting the air and causing numerous environmental problems. Effective dust control is essential for the success of your industry.
Solution: DustDown 369, CSS
DustDown 369 and CSS are effective solutions for addressing the dust issues mentioned above. DustDown 369 is a material for effective dust control that can be applied to roads to bind dust particles, preventing them from becoming airborne and spreading.
Meanwhile, CSS (Chemical Stabilizing Solution) functions to stabilize the road surface, reducing abrasion and dust formation caused by heavy vehicle movement and wind.
These solution products help you address critical issues caused by dust as described above.
4. Problem: Grease Quality
Of course, low-quality grease or grease that does not meet specifications can lead to lubrication failures. It cannot handle high temperatures, heavy loads, high speeds, contaminants, and other extreme challenges.
Solution: Molykote / Dow / LE
High-quality greases like Molykote, Dow, and Lubrication Engineers (LE) are the right and effective solutions for lubrication systems in challenging conditions.
These grease formulas are designed to handle high pressure, extreme temperatures, and contamination from dust and limestone particles, ensuring optimal performance of machines and equipment.
Please contact us on WhatsApp for further information or consultation.
5. Problem: Floor (Slippery and Damaged)
The issue of slippery and damaged floors in the quenching process unit within the cement industry involves significant risks to worker safety and operational efficiency. Milling and raw material transportation activities, such as limestone and clay, often cause material spills, oil, and water, making the floor slippery and dangerous for workers walking or operating machines in the area.
Heavy loads from milling equipment and moving vehicles can cause structural damage to the floor, such as cracks and wear. Poor floor conditions can increase the risk of workplace accidents and hinder operational activities, requiring special attention in maintenance and repair..
Solution: EonCoat 551 / EonCoat 470
Special coating products that, after curing, produce a very hard layer. Resistant to impact, oil, and chemicals, making it durable and non-slippery.
These products can be applied to new construction surfaces or used as a primer for anti-corrosion coating systems in buildings, offshore, petrochemical, mining, chemical industries, and others. The resulting coating provides maximum protection against harsh environmental conditions, ensuring the longevity and reliability of the coated structure.
6. Problem Quenching Process: Water Treatment
The issue of water treatment in the quenching process unit within the cement industry includes challenges in managing the water used in various production processes, such as cooling and cleaning. The water used is often contaminated by fine particles from raw materials such as limestone and clay.
If these contamination issues are not properly addressed, they can disrupt smooth operations, ultimately increasing operational costs.
Solution: Coagulants and Flocculants
Eonchemicals offers high-quality coagulants and flocculants to address the issues mentioned above. These solution products function to precipitate contaminants present in the water.
Coagulants are used to bind small particles into larger ones. Flocculants are intended to perfect the process by gathering the already larger particles into even bigger flocs, making them easier to settle.
By using a combination of coagulants and flocculants, contaminants such as limestone and clay in the water can be precipitated more effectively and efficiently.
Please consult your issues with us via WhatsApp chat now.
7. Problem: Boiler
The issue of boilers in the quenching process unit within the cement industry includes challenges in maintaining optimal performance and operational reliability of boilers used to provide steam or heat in the production process.
The most common boiler problems are corrosion, scaling, and fouling, primarily caused by feed water quality that does not meet suitability standards.
The presence of corrosion, scaling, and fouling problems can cause component damage, reduce heat transfer efficiency, and increase fuel requirements.
Solution: Eon Boiler Chemicals
Eon Boiler Chemicals is an effective solution package to address boiler problems in the quenching process unit within the cement industry. These boiler chemicals are specially formulated to address scaling, corrosion, and fouling issues.
With the correct application method and dosage, Eon Boiler Chemicals will help maintain optimal performance and operational reliability of the boiler.
Do not hesitate to contact us for product details, application methods, and the correct dosage to effectively solve your field problems.
| Check out clinkerisation process problems and solutions on this site
8. Problem: Cooling Tower
The issue of cooling towers in the quenching process unit within the cement industry involves challenges in maintaining optimal cooling efficiency during the production process. Cooling towers function to dissipate heat generated during operations but often experience issues such as scaling, rust, and algae formation on the tower surface.
Additionally, mineral buildup and deposits from the water used for cooling can reduce heat transfer efficiency, increase water consumption, and affect the quality of water reused in the process.
Solution: Eon Cooling Tower Chemicals
Eon Cooling Tower Chemicals is a solution package to address various problems in cooling towers. These solution products include EonBac GEO 9910, EonLine AG 5770, and EonScale T 2511.
Eon Cooling Tower Chemicals are innovative and effective solution products. Their formulas are specifically designed to address various issues related to cooling efficiency and water quality, including solutions for corrosion, scaling, algae, and other problems.
Please chat with us on WhatsApp for further information, usage instructions, and the correct dosage according to your field needs.
| Read grinding process problems and solutions on this site
9. Problem: Metal Repair
The issue of metal repair in the quenching process unit within the cement industry often arises due to extreme conditions in the kiln and other equipment exposed to constant and repeated high temperatures.
Equipment such as kilns, preheaters, and coolers experience significant wear and corrosion due to exposure to extreme temperatures and chemicals in the process. Damage to these metal parts can disrupt the cement production process, increase maintenance and downtime costs for repairs, and threaten operational safety.
Solution: Metbond 581
Metbond 581 is a build & repair compound for rebuilding damaged (worn or leaking) metal components due to erosion and corrosion. This product can be easily applied to corroded or damaged components without the need for welding, making it safer and more convenient to use.
Metbond 581 is ideal for various components such as pump bodies, impellers, propellers, grates, valves, tube sheets, water tanks, rudders, and HE components. Metbond 581 produces a layer with high resistance to abrasives and erosion, as well as other physical impacts.
| Read also power plant problems and solutions
Discuss quenching process problems in your industry via chat WhatsApp Eon, now.
Consult with EON Now
We are ready to listen and provide the right chemical solution for you. Consultation with our experts is free!
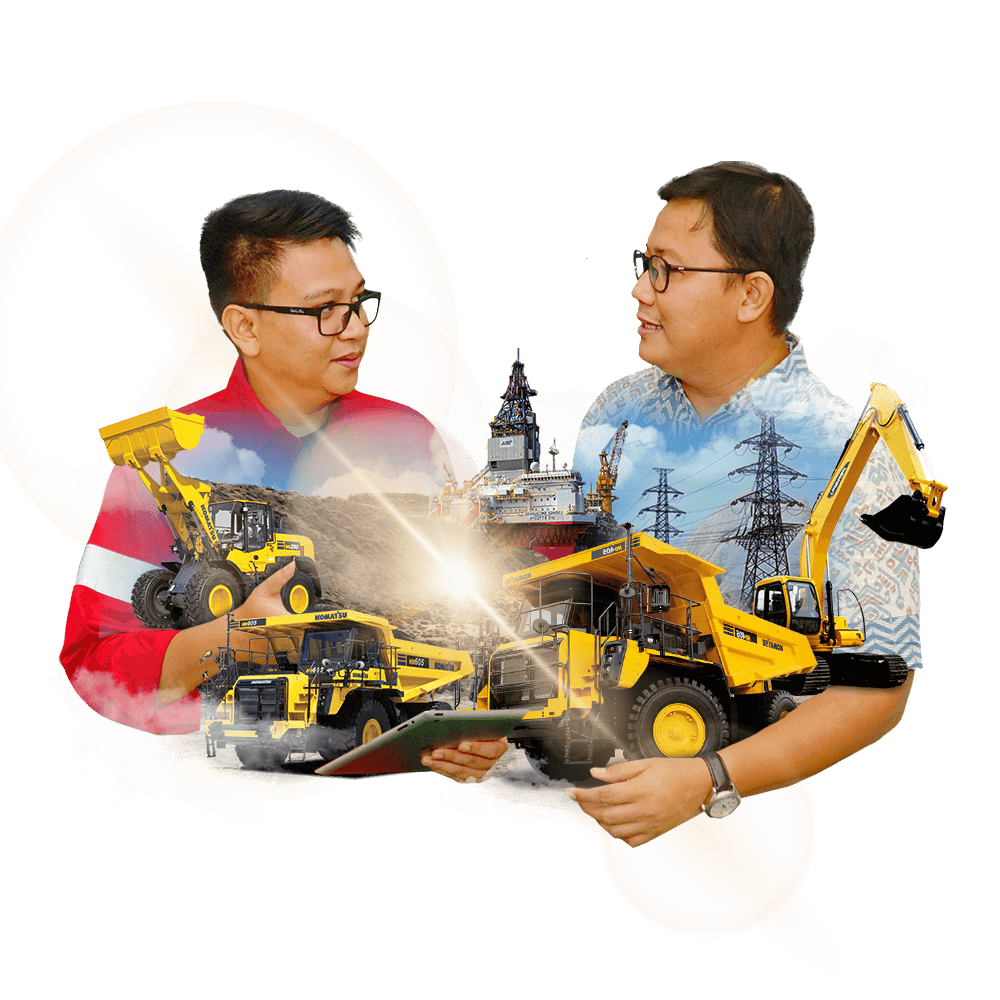