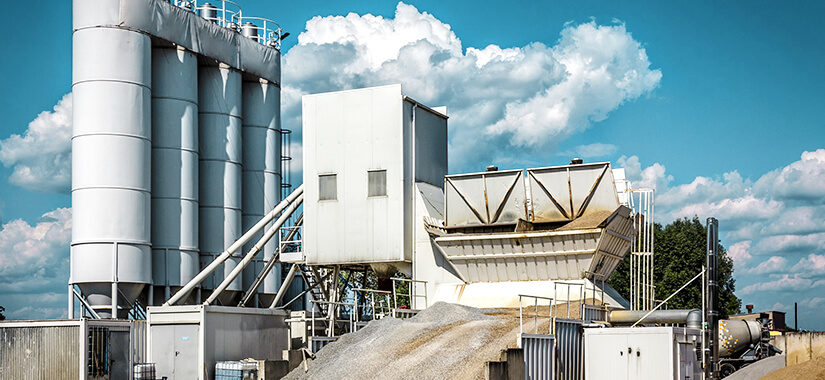
The power plant in the cement industry plays a crucial role as the primary source of electrical energy required for all production processes, from raw material grinding to clinker burning. This power plant typically utilizes power generation systems such as boilers and turbines to produce heat and electricity.
Operational efficiency and reliability of the power plant are vital in the cement industry due to the high energy consumption and the need for a consistent and stable electricity supply.
Common problems found in this unit, along with their solutions from Eonchemicals, include:
1. Problem: Coal Spontaneous Combustion
Spontaneous combustion of coal in cement industry power plants occurs when stored coal undergoes spontaneous oxidation, generating sufficient heat to ignite without an external flame.
If not promptly addressed, spontaneous combustion can lead to significant fires, damage facilities, disrupt operations, and pose serious safety hazards to workers.
Solution: FireShield 108 / Cofirex
FireShield 108 / Cofirex is an innovative and effective solution for the problem of spontaneous coal combustion in cement industry power plants. This product is specially designed to enhance safety and efficiency in boiler operations.
FireShield 108 has excellent wetting capabilities, bringing more water to wet and cool the coal, thus extinguishing fires more quickly. It also has excellent penetration properties, reducing the surface tension of the coal, allowing water to penetrate the stockpile crevices and extinguish the fire rapidly.
Additionally, FireShield 108 prevents re-ignition for a longer period by interrupting the chemical reaction of spontaneous combustion. The use of this product is very economical as it effectively extinguishes fires with a concentration of only 1-3%. FireShield 108 is safe for users and the environment as it is water-based, non-toxic, biodegradable, and easy to use.
2. Problem: Coal Dust
The issue of coal dust in cement industry power plants involves challenges in managing the dust generated by coal. This dust can spread into the surrounding air and, if not properly managed, can cause air pollution around the plant, disrupt local air quality, and pose potential health issues for workers and the surrounding community.
Additionally, managing coal dust is crucial to maintaining cleanliness and operational safety within the plant, reducing machinery damage caused by uncontrolled dust accumulation.
Solution: DustDown 369, CSS
DustDown 369 and CSS can be effective solutions for the problem of road dust in raw material milling in the cement industry as both are designed to control and suppress dust generated by transportation and milling activities.
DustDown 369 is an effective dust suppressant that can be applied to roads to bind dust particles, preventing them from becoming airborne and spreading. CSS (Chemical Stabilizing Solution) works by stabilizing road surfaces, reducing abrasion and dust formation caused by heavy vehicle movement and wind.
Please chat with us on WhatsApp for further discussion.
3. Problem: Prevention of Coal Spontaneous Combustion
The issue of preventing spontaneous coal combustion in cement industry power plants involves efforts to reduce the risk of fires caused by spontaneous ignition or excessive heating of coal.
Effective prevention is necessary to minimize fire risks, protect plant infrastructure, and ensure sustainable operational safety in the cement industry.
Solution: CoalGuard 535
CoalGuard 535 is an effective solution for the problem of preventing spontaneous coal combustion in cement industry power plants as it is specifically designed to reduce the risk of spontaneous ignition in coal.
CoalGuard 535 works by suppressing oxidation and stabilizing coal during storage and transportation, thus reducing heat accumulation that can lead to spontaneous combustion.
By using CoalGuard 535, fire risks can be minimized, ensuring the safety and reliability of power plant operations, and protecting plant infrastructure from fire damage.
Please chat with us on WhatsApp for more satisfactory information.
4. Problem: Ceramic Insulator Cleaner
The issue of cleaning ceramic insulators in cement industry power plants involves keeping insulators clean and free from contaminants that can reduce the efficiency and safety of the electrical system.
Ceramic insulators are used to support and separate electrical conductors, and if contaminated by dust, dirt, or other pollutants, can cause a decrease in insulation performance and even trigger sparks or electrical leakage.
Solution: IsoClean
IsoClean is an effective solution for the problem of cleaning ceramic insulators in cement industry power plants as it is specifically designed to clean insulators from dust, dirt, and other pollutants that can interfere with electrical insulation performance.
IsoClean has a formula that can remove contaminants without damaging the ceramic surface, ensuring the insulators remain clean and function optimally. By using IsoClean, the risk of decreased insulation performance, sparking, or electrical leakage can be minimized, thereby enhancing the operational efficiency and safety of the electrical system in the power plant.
Do not hesitate to chat with us on WhatsApp for additional information.
5. Problem: Transformer Oil
The issue of transformer oil in cement industry power plants relates to the quality and performance of transformer oil used for cooling and insulating electrical transformers. Transformer oil that does not meet quality standards poses many risks.
This problem can cause overheating, reduce transformer efficiency, and increase the risk of operational damage or failure
Solution: Nynas Nitro Libra
Nynas Nitro Libra is an effective solution for the problem of transformer oil in cement industry power plants as it is specifically designed to provide optimal cooling and insulation performance in electrical transformers.
Nynas Nitro Libra has good thermal stability, thus maintaining oil quality and performance for a longer period. This product also has good resistance to contamination and degradation, helping to reduce the risk of overheating and decreased transformer efficiency. Electrical transformers operate safely and efficiently, increasing the reliability of the electrical system and reducing the risk of damage and maintenance costs.
6. Problem: Slippery and Damaged Floors
The issue of slippery and damaged floors in the power plant area in the cement industry poses significant safety risks for workers and equipment users. Exposure to water, oil, or chemicals can make floors slippery, leading to serious accidents such as slips or falls, potentially resulting in injuries and unwanted downtime.
Heavy activities such as heavy equipment operations and material transportation can also cause wear and damage to floors. This damage increases the risk of accidents and can shorten the floor’s lifespan, affecting overall operational efficiency.
Solution: EonCoat 551 / EonCoat 470
EonCoat 551 and EonCoat 470 are effective solutions for the problem of slippery and damaged floors in the power plant area in the cement industry. Both products are protective coatings specifically designed to enhance safety and extend the lifespan of floors. They provide durable protection against abrasion, impact, oil, chemicals, and heavy pressure from equipment and materials operating on them.
By applying EonCoat 551 or EonCoat 470, floor surfaces can be made rougher, reducing slipperiness and the risk of slipping. These products help create a safer and more efficient work environment, reducing the risk of accidents and unwanted downtime.
7. Problem: Electrical Panel Cleaner
The issue of cleaning electrical panels in cement industry power plants involves challenges in keeping electrical panels clean and free from dust, dirt, and other residues that can disrupt electrical performance. Dirty electrical panels can lead to contaminant buildup that reduces electrical flow efficiency, increases the risk of short circuits, and even triggers fires.
Additionally, dust and dirt can cause a decrease in the sensitivity of sensors and control devices, disrupting automatic operations and electrical system settings. Maintaining the cleanliness of electrical panels is crucial to ensuring the reliability and safety of the electrical system and preventing unwanted downtime.
Solution: EonCont 211, EonCont 205
These solution products are electric contact cleaners, which are chemical cleaners specifically designed for electrical equipment. These products are ideal for cleaning electrical instrumentation or electronic equipment from dirt, dust, grease, oil, or water, ensuring the equipment remains functional and safe.
These electric contact cleaners have various features and benefits, such as not damaging plastic, rubber, or enamel insulation, and not leaving a film residue. They also have high dielectric strength, are non-conductive, non-corrosive, non-flammable, and meet industrial safety standards
| Next, please read clinkerisation process problems and solutions
Let’s discuss about power plant problems with our WhatsApp chat to get effective solutions.
Consult with EON Now
We are ready to listen and provide the right chemical solution for you. Consultation with our experts is free!
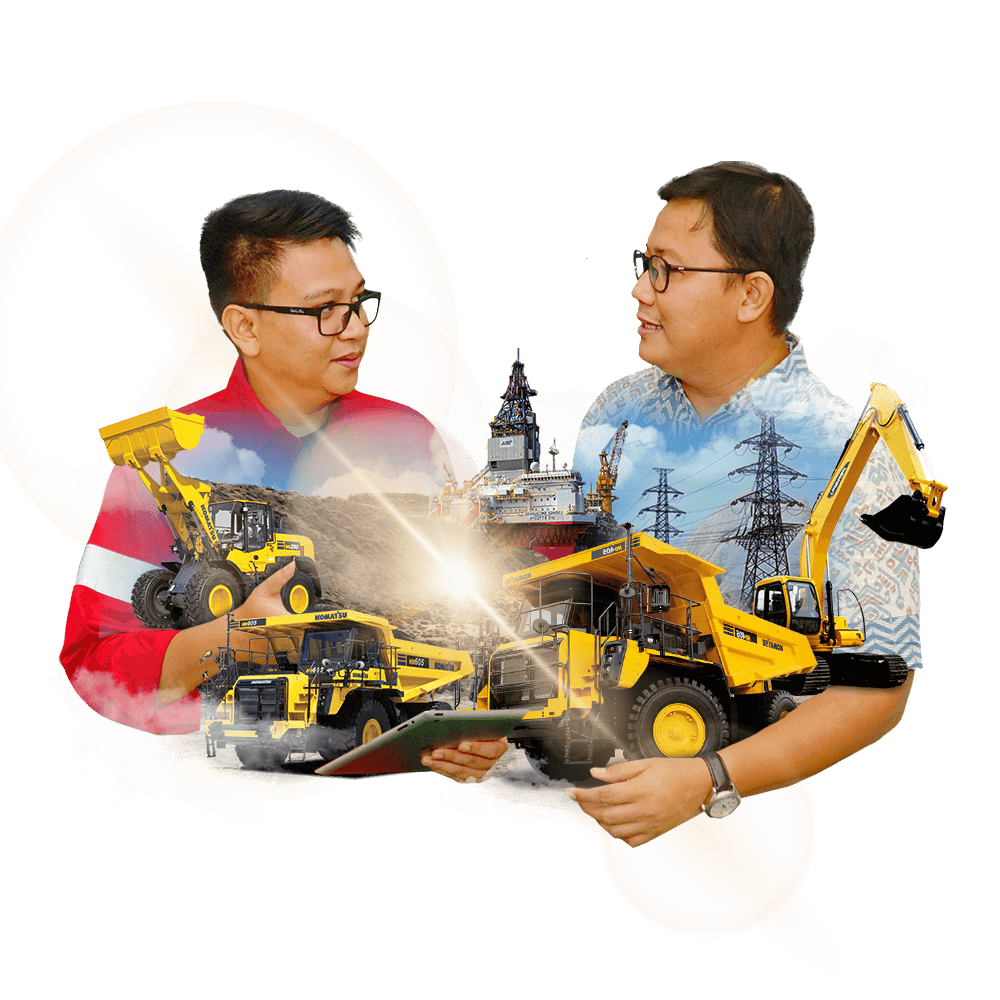