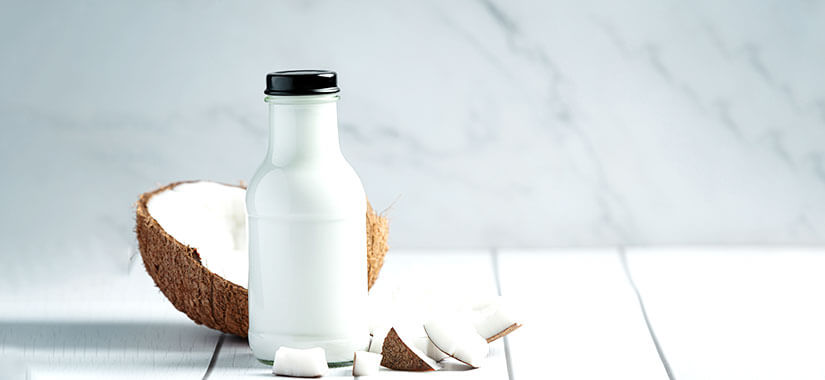
A good coconut milk packaging process is necessary to maintain the quality and durability of the product. Please take a look at some of the problems and solutions offered by us as experts in specialty chemicals.
1. Problem: Printing Machine/Parts Contaminated with Ink
Ink contamination can interfere with print quality on the packaging, leading to smudged or uneven results that diminish the product’s appearance. If you’re dealing with this issue, EonRollink 388 is the solution you can count on..
Solution: EonRollink 388
This product is a solvent-based ink cleaner formulated effectively to clean oil-based inks. The EonRollink 388 formula is suitable for cleaning UV printing machines as well as general printing machines.
With its quick and effective action, EonRollink 388 is the right solution for cleaning various types of oil-based inks.
EonRollink 388 is safe for routine application, including safe for application on rubber roll blankets in printing machines, and it does not cause rust problems on any type of metal. Please contact us for more information.
2. Problem: Adhesive Residue on Labeling Machines
Adhesive residue on labeling machines during the coconut milk packaging process can cause serious negative impacts. Leftover adhesive on the labeling machine can cause blockages and mechanical disruptions, thereby reducing production efficiency and speed.
Experiencing this issue? Contact Eonchemicals for the application of EonSolv 135 as an effective solution.
Solution: EonSolv 135
EonSolv 135 is a formula for general maintenance cleaning, including cleaning dirty labeling machines. This powerful formula can remove residues such as adhesives, grease, lubricating oils, rust, and other contaminants. EonSolv 135 is not suitable for application on rubber materials.
In addition to its ability to quickly and economically clean residues, this cleaning product has a high flash point, making it non-flammable at room temperature.
Another benefit is that this product does not cause corrosion and is suitable for all types of metals. Furthermore, EonSolv 135 leaves no residue, so there is no need to rinse after application.
3. Problem: Grease/Oil on Chains Contaminating the Product
Grease or oil on chains contaminating the product during the coconut milk packaging process can cause serious consequences. This contamination can occur because the lubricant used is a wet lubricant, which can drip.
The solution: Use dry lubricant! Contact us to get it.
Solution: Molykote AFC
Molykote AFC known as anti-friction coating is the right solution to overcome it. This lubricant product is also called a dry lubricant, so it does not flow and drip and contaminate food products.
4. Problem: Short Regreasing Period
The cause is usually the quality of the grease, which may not perform well under the operational conditions at your site, leading to quick degradation of its effectiveness.
The solution is to use long-lasting grease that can withstand challenging operational conditions.
| Read coconut milk filling problems and solutions in your industry
Solution: LE Lubricant
LE Lubricant is an excellent solution to address the problem of frequent regreasing in this unit. This lubricant’s formula is designed to last longer under extreme operational conditions, with high thermal stability and resistance to oxidation. This ensures that the grease remains effective in lubricating machine components at high temperatures and heavy loads.
| Read coconut water capping and packaging problems and solutions
Thus, using LE Lubricant can reduce the frequency of regreasing. It provides more consistent and optimal lubrication, reduces operational costs, minimizes machine downtime, and maintains production efficiency.
Consult with EON Now
We are ready to listen and provide the right chemical solution for you. Consultation with our experts is free!
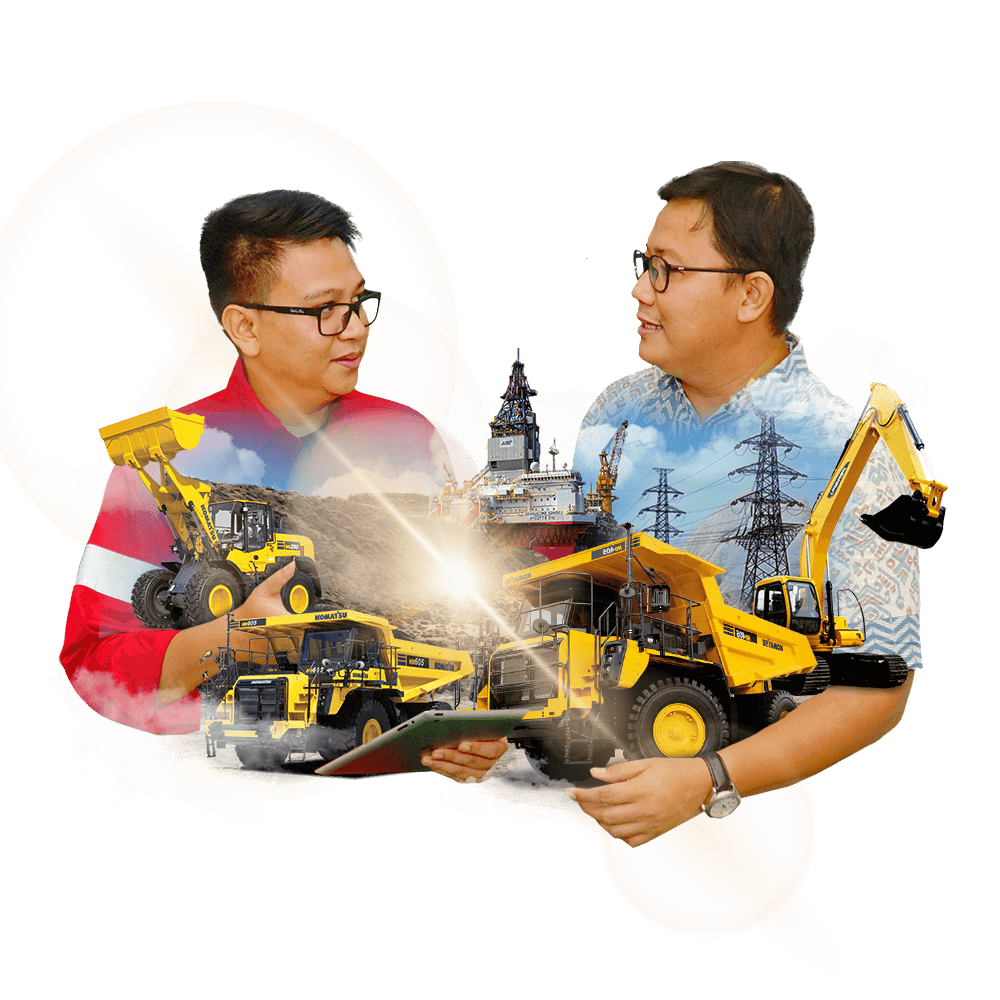