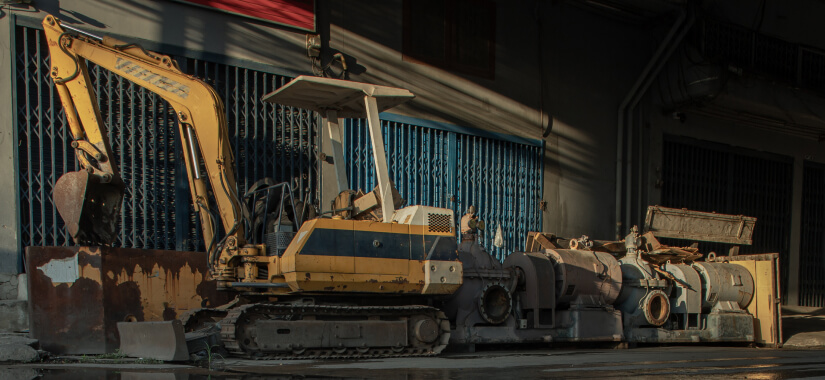
- 1. Problem: Oil Spills in the Workshop
- 2. Problem: Dirty Floors and Units
- 3. Problem: Heavy Dirt
- 4. Problem: Dirty Spare Parts
- 5. Problem: Dirty Electric Motors
- 6. Problem: Dirty Piston and Carbon Deposits
- 7. Problem: Rusty Parts
- 8. Problem: Cleaner Robowash
- 9. Problem: Dirty and Rusty Internal Radiators
- 10. Problem: Existing Radiator Coolant Does Not Last Long
- 11. Problem: Hands Dirty with Oil & Grease
- 12. Problem: Yellow Stains on LV Units
- 13. Problem: Rusty Bolts Hard to Remove
- 14. Problem: Rusty and Frequently Breaking Wire
- 15. Problem: Dirty Electrical Equipment
- 16. Problem: Floor Coating Peels Off Quickly
- 17. Problem: HD Turn Table Often Rusts
- 18. Problem: Antiseize
In the mineral mining industry, an HD Workshop is a facility for the maintenance and repair of heavy equipment used in mining operations. It is typically equipped with advanced tools and trained professionals to perform routine maintenance, repairs, and reconditioning of machinery and heavy equipment components such as mining trucks, excavators, and loaders..
The common problems encountered in this workshop and their solutions are as follows:
1. Problem: Oil Spills in the Workshop
Oil spills in the workshop are a serious issue that can cause various problems. These spills can make surfaces slippery, increasing the risk of accidents and injuries for workers.
Additionally, spilled oil can seep into the ground or drainage systems, polluting the surrounding environment. Spills can also damage equipment and workshop floors.
Solution: Oil Absorbent | Spill Kit
A spill kit is a set of equipment designed to handle oil, chemical, and other spills. This kit includes various types of oil absorbents, goggles, gloves, and waste collection bags for used absorbents. Eon spill kits can handle various types of spills quickly and efficiently.
Eonchemicals offers a variety of spill kits, allowing you to choose the one that best suits your workshop’s needs.
For recommendations on the right type of spill kit, please consult with us.
2. Problem: Dirty Floors and Units
Dirty floors and units in a work environment such as a workshop or factory can have various negative impacts. Floors dirty with dust, oil, or chemicals not only damage equipment and disrupt operational efficiency but also increase the risk of workplace accidents.
Dirty machinery units can overheat or malfunction due to dirt buildup that obstructs ventilation and cooling. Moreover, a dirty work environment can lower employee morale and productivity, as well as increase maintenance and repair costs due to more frequent equipment damage.
Solution: QuickBreak 600
QuickBreak 600 is a quick-break cleaning chemical designed to efficiently clean oil, grease, and other dirt.
As a water-based cleaning chemical, QuickBreak 600 has several advantages, primarily its quick-break capability, allowing for fast and efficient cleaning without residue.
Additionally, this cleaning chemical is environmentally friendly, making it safe for the surrounding ecosystem. User safety is, of course, a priority. With excellent cleaning power, this product can tackle various types of dirt and ensure optimal cleaning results.
3. Problem: Heavy Dirt
Heavy dirt such as oil, grease, industrial dust, and chemical residues can accumulate on floors and equipment surfaces, making the work environment unsafe and unhygienic.
Heavy dirt can also damage machines and tools, reducing their lifespan. The accumulation of heavy dirt complicates inspection and routine maintenance processes, which can ultimately negatively impact the overall productivity and performance of the workshop.
Solution: EonClean 500
EonClean 500 is a solvent-based degreaser, a highly effective cleaning chemical formulated specifically to clean stubborn dirt such as oil, grease, asphalt, and grime from metal surfaces and other areas.
This solvent-based degreaser is ideal for general cleaning, automotive, marine, and mining industries. Its effectiveness in removing tough dirt makes it a solution for handling heavy dirt.
Note: This product is not recommended for cleaning dirt on rubber or other aliphatic hydrocarbon compounds.
4. Problem: Dirty Spare Parts
In an HD workshop in a mineral mine, dirty spare parts are often found. Dirty spare parts must be thoroughly cleaned; otherwise, they will cause a decrease in the efficiency and performance of heavy equipment. Dirt such as dust, mud, or oil can interfere with the efficiency of component functions.
Additionally, dirty spare parts can experience premature damage, increasing downtime and reducing productivity, as well as increasing operational costs.
Solution: EonSolv 135
EonSolv 135 is a general cleaning degreaser suitable for general maintenance cleaning, including handling dirty spare parts. This cleaning chemical is effective in removing dirt such as glue, grease, lubricating oil, rust, and other types of dirt from spare parts. Moreover, this cleaning chemical can protect and extend the life of spare parts. It is easy to use, but keep in mind that this product is not suitable for rubber materials.
EonSolv 135 cleans dirt quickly and economically. It has a high flash point, so it will not ignite at room temperature. It is safe because it does not cause rust and is safe for all types of metals.
This cleaning solution does not leave residue, so no rinsing is required after application. Please chat with us via WhatsApp for more information.
5. Problem: Dirty Electric Motors
A dirty electric motor is a condition where the exterior and interior of the electric motor are filled with dust, oil, or other contaminants. This can disrupt motor performance, reduce efficiency, and accelerate component wear. Accumulated dirt can increase operating temperature and the risk of overheating.
Additionally, dirt can cause electrical problems such as short circuits and reduce the lifespan of the motor.
Solution: EonMotor 100
EonMotor 100 is an electric motor cleaning fluid made from a solvent mixture designed to clean electric motors and dynamos from dust, oil, and grease. This product is highly effective in removing contaminants.
When used correctly, this product can help keep electric motors clean and functioning well, extending their lifespan and improving overall performance. Regularly cleaning electric motors with the right cleaning fluid is an important step in preventive maintenance that can save on repair and replacement costs in the future.
| Read also a table of coal mining industry problems and solutions
6. Problem: Dirty Piston and Carbon Deposits
This condition occurs when pistons in vehicle engines are covered with carbon deposits and dirt. This can interfere with piston movement, reduce combustion efficiency, and cause a decrease in engine performance.
Accumulated carbon deposits can also increase friction and wear on pistons and cylinder walls, accelerating component damage and increasing fuel consumption.
Solution: EonCarb 544
EonCarb 544 is a water-based carbon removal chemical effective in removing carbon residue from combustion, varnish, oil, and grease from metal surfaces. This product is suitable for addressing dirty and carbon-encrusted pistons.
This carbon cleaner consists of a mixture of active ingredients that can quickly penetrate and dissolve, ensuring thorough and efficient cleaning, so various contaminants attached to the piston can be optimally removed.
7. Problem: Rusty Parts
Rusty parts generally occur due to exposure to air and humidity. Rust damages metal surfaces, reduces strength, causes wear, and leads to part failure. Additionally, rust can disrupt mechanical performance, shorten lifespan, and increase the risk of further damage.
Solution: EonRust 501
EonRust 501 is a rust remover chemical formulated to clean rust on iron, clean machine rust, and prepare metal surfaces for repainting. This product is suitable for addressing rusty parts in your HD workshop.
This cleaning chemical formula consists of a mixture of acids and surfactants that work synergistically to dissolve rust efficiently. This combination ensures that the metal is not only clean from rust but also ready to receive a new coat of paint, providing additional protection against corrosion.
8. Problem: Cleaner Robowash
Cleaner Robowash is an automatic cleaning machine used to clean various industrial equipment.
The problem we found in the field is that the use of cleaning agents in this cleaning machine is less effective because of excessive foam and unsatisfactory results.
The use of inappropriate cleaning chemicals can also damage machine parts, shorten their lifespan, and require higher repair costs.
Solution: Alklin 220 and Alklin 110
We recommend these cleaner chemicals as a solution for your automatic cleaning machine. With excellent cleaning power and minimal foam, the washing process with the machine becomes more effective.
Another benefit is that it dissolves easily and leaves no residue, avoiding future problems. Suitable for all types of automatic cleaning machines.
Please contact us for recommendations on the most suitable type of Alklin for your cleaning machine.
9. Problem: Dirty and Rusty Internal Radiators
A dirty and rusty internal radiator is a condition where the inside of the radiator is filled with dirt and rust deposits.
This can cause the radiator to overheat. Rust and dirt can damage the internal walls of the radiator, causing leaks and shortening its lifespan.
Solution: EonRadflush 410
This solution product contains corrosion inhibitors and mild acids. A formula specifically designed to clean the inside of radiators. This substance effectively removes rust, scale, and other dirt deposits, ensuring the radiator remains clean and free from obstructions that can disrupt the coolant flow. With this composition, the radiator cleaner can restore and improve the cooling efficiency of the engine.
The corrosion inhibitor in this solution product cleans and prevents future rust formation. This is crucial for maintaining the internal pipes of the radiator to keep them clean and functioning optimally. Safe to use on various metals such as iron, aluminum, and copper, so it does not damage radiator components during the cleaning process. Regular use of radiator cleaner, once every three months, can help maintain the radiator in optimal condition.
A clean radiator means the engine heat can be controlled better, reducing the risk of overheating and extending the overall engine life. With proper maintenance, cooling efficiency will increase, and vehicle performance will remain optimal.
10. Problem: Existing Radiator Coolant Does Not Last Long
This problem occurs because the radiator coolant currently in use loses its effectiveness faster than expected. This can be due to low-quality coolant, continuous exposure to high temperatures, or contamination in the cooling system. When the coolant is no longer effective, it cannot efficiently absorb and transfer heat from the engine, causing the engine to overheat.
Solution: RadCool 200
RadCool 200 is an ethylene glycol radiator coolant, an extended-life radiator fluid based on ethylene glycol specifically formulated for heavy-duty engines. This product combines Organic Acid Technology (OAT) and nitrite corrosion inhibitors, providing excellent protection against corrosion in the engine and cooling system.
RadCool 200 is a ready-to-use product, requiring no pre-dilution with water.
11. Problem: Hands Dirty with Oil & Grease
This problem is a common challenge faced by workers in the mining industry. Hands exposed to oil and grease are not only difficult to clean but can also cause skin irritation and unpleasant odors.
Additionally, oil and grease on hands can dirty tools, equipment, and other surfaces, reducing work efficiency and increasing the risk of accidents. Without an effective cleaning solution, this problem can negatively impact worker health and the quality of the work environment.
Solution: EonHand 270
EonHand 270 is an innovative solution for dirty hands full of oil and grease. This hand soap is specially formulated without solvents but is still capable of removing grease, oil, paint, ink, asphalt, glue, tar, and other stubborn dirt.
EonHand 270 is a waterless hand cleaner, meaning it does not require water to clean your hands thoroughly and hygienically. Its ability to tackle various types of dirt makes it far more effective than regular soap.
This product not only improves work efficiency by quickly and easily cleaning hands but also supports worker health by reducing the risk of skin irritation from chemical residues.
12. Problem: Yellow Stains on LV Units
Yellow stains on LV (Low Voltage) units can cause various issues. These stains often appear due to oxidation, heat exposure, or chemical reactions with certain materials. These stains not only affect the aesthetics and cleanliness of the unit but can also impact the performance and reliability of the LV unit.
Without the right solution, this problem can negatively affect the performance, lifespan, and operational safety of the LV unit.
Solution: EonBright 333
This product serves as a stain/scale remover, safe for all types of metals, and also functions as a rust remover. Please chat with us via WhatsApp for further consultation.
13. Problem: Rusty Bolts Hard to Remove
Rusty bolts that are difficult to remove are a common problem in the mining industry. A corrosive environment, including humidity, dust, and chemicals, accelerates the corrosion process on bolts.
If bolts are rusty, they become difficult to loosen, hindering routine maintenance and repairs.
Solution: EonPen 111
EonPen 111 is a penetrating fluid, a liquid capable of penetrating, lubricating, and releasing rust. This solution is suitable for loosening bolts that are difficult to remove due to rust.
Its ability to penetrate well into bolt threads makes this product an ideal choice for loosening rusty bolts. Please contact us for more information via WhatsApp chat..
14. Problem: Rusty and Frequently Breaking Wire
Common issues with wire ropes include rust and wear due to friction. Corrosion is caused by exposure to a corrosive environment, and the wire rope lacks adequate protection. Wear occurs due to continuous friction, while the lubricant used is not supportive.
Solution: EonWire 230 & 237
The solution to the above problems is EonWire. This solution product is a wire rope lubricant & inhibitor, a combination of lubricant and anti-rust for effective wire rope protection. This solution product adheres strongly to the surface of the wire sling, protecting it from rust and wear due to friction.
EonWire does not melt at high temperatures and pressures, providing optimal protection for your wire rope in extreme conditions.
15. Problem: Dirty Electrical Equipment
Dirty electrical equipment can cause various serious problems. Dirt such as dust, oil, and other residues can disrupt the performance and efficiency of the equipment, cause overheating, and increase the risk of short circuits or component damage.
Additionally, dirt can shorten the lifespan of electrical equipment. In an industrial environment, dirty equipment can also disrupt production processes and cause costly downtime.
Solution: EonCont 211
EonCont 211 is an electric contact cleaner, a cleaning fluid specifically designed for electrical equipment. This product is ideal for cleaning electrical instrumentation or electronic equipment from dirt, dust, grease, oil, or water, ensuring the equipment remains functional and safe. Features and benefits include:
- Does not damage plastic, rubber, or enamel insulation
- Leaves no film residue
- High dielectric strength, non-conductive
- Non-corrosive and non-flammable
- Meets industrial safety standards
16. Problem: Floor Coating Peels Off Quickly
This problem can be caused by inadequate surface preparation before application, resulting in poor adhesion of the coating. Using the wrong type of coating for the floor or environmental conditions can also be a cause.
The coating used for workshop floors must have characteristics resistant to chemicals, oil, and impact.
Solution: EonCoat 551
EonCoat 551 is a two-component anti-rust epoxy coating. Its main characteristic is that after curing, it produces a very hard layer with high resistance to impact and chemicals. This product can be applied to new construction surfaces or used as a primer for maintaining anti-rust coating systems in buildings, offshore, petrochemical, mining, chemical industries, and others.
| Read also mining reclamation problems and solutions
17. Problem: HD Turn Table Often Rusts
Rust problems that often occur on HD (Heavy Duty) turn tables can be caused by several factors. Continuous exposure to moisture, water, and harsh environmental conditions, such as rain or high salinity, accelerates the oxidation and corrosion process on the turn table’s metal surface.
Additionally, the use of improper lubricants or protective coatings can contribute to this problem. Untreated rust can reduce the operational efficiency of the turn table, shorten its lifespan, and increase the risk of damage requiring costly repairs or component replacement.
Solution: EonRust 501
EonRust 501 is a rust remover, a special chemical used to clean rust and prepare metal surfaces for recoating. This product is suitable for addressing frequently rusting turn tables.
This cleaning chemical contains a mixture of acids and surfactants that work synergistically to dissolve rust efficiently. This combination ensures that the metal is not only clean from rust but also ready to receive a new coat of paint, providing additional protection against corrosion.
| Read hauling road problems and solutions on this site
18. Problem: Antiseize
Antiseize-related problems arise when components frequently exposed to high heat, pressure, or extreme environmental conditions, such as bolts, nuts, and fittings, experience excessive binding or locking. Without the proper antiseize lubricant, metals can stick together due to thermal expansion or corrosion, making components very difficult to remove.
This problem can cause damage to the parts, requiring extra effort, time, and cost for repairs or replacements. Ineffective or absent antiseize increases the risk of wear, thread damage, and equipment failure.
| Read effective conveyor problems and solutions
Solution: Molykote 1000 & Molykote GN Plus
Molykote 1000 is a solid lubricant paste that does not contain lead or nickel. This specialty lubricant product is a solution for bolt connections exposed to temperatures up to 650°C (1202°F), providing protection against corrosion.
Molykote 1000 is applied after assembly or at the start of operation, especially when bolts need to be retightened or removed. This specialty lubricant product ensures consistent pre-stressing force and is required if a uniform and stable friction coefficient of the lubricant is desired.
Molykote GN Plus is a solid lubricant paste for assembling and operating metal components, including bolt installation. This solution product is suitable and effective for preventing corrosion, handling friction and scratches, and serving as a good anti-corrosion agent.
Molykote GN Plus also reduces fretting corrosion formation, facilitates disassembly, and can be applied to high-load conditions. With a low friction coefficient and protection from stick-slip, this lubricant product can enhance efficiency.
| Read also tire workshop problems and solutions
Consult HDW (Heavy Dutty Workshop) problems in your mineral mining industry to get the right solution from Eonchemicals.
Consult with EON Now
We are ready to listen and provide the right chemical solution for you. Consultation with our experts is free!
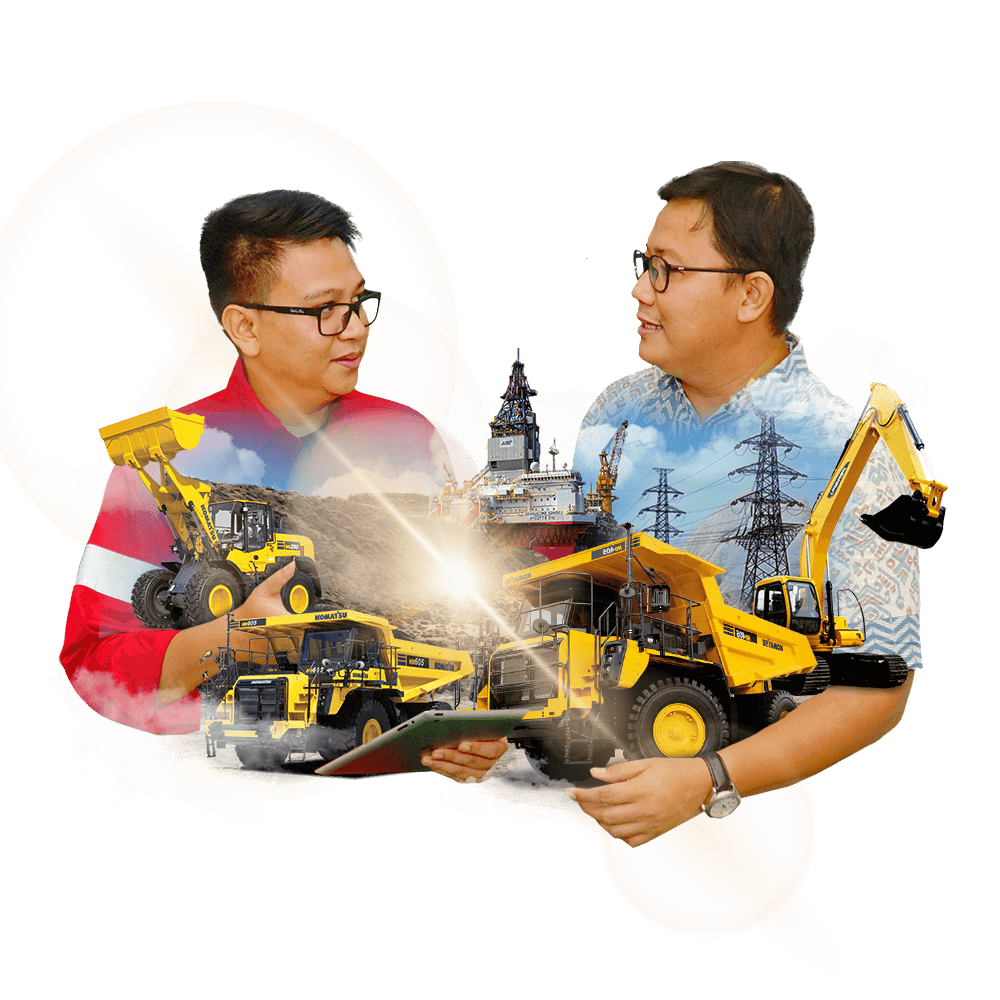