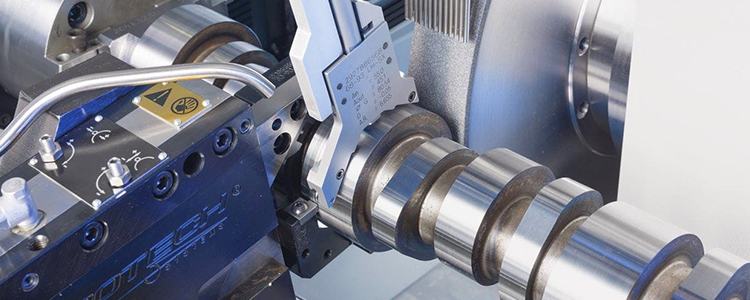
Grinding wheels are used in th e grinding process, which involves cutting hard materials to achieve a good super finish, high accuracy, and precision.
Grinding wheels that are used continuously will experience wear and changes in shape. Therefore, a dressing process is needed to restore the grinding wheel’s profile so it can be used again. The dressing process can be repeated multiple times until a certain point when the grinding wheel must be replaced.
A problem to be noted is overly rapid dressing due to the grinding wheel wearing down easily. If this happens, the lifespan of the grinding wheel becomes short. This is wasteful and should not occur, right?
Solution
The solution to extend the dressing interval of the grinding wheel is to use a suitable coolant. The selection of coolant for grinding applications should consider the following aspects:
- Lubricity
- Wetting
- Cooling
- Compatibility with the abrasive system
- Coolant cleanliness
Success Story
One of our customers experienced a problem where the grinding wheel had too short a dressing cycle and needed frequent replacement, resulting in suboptimal productivity.
We then conducted a more detailed problem investigation with our engineering and production teams, with the following results:
- The current dressing cycle can only reach 30 pieces
- The coolant in the tank and inside the machine is dirty
- The coolant is mixed with tramp oil, making it sticky and deteriorating quickly
Solution
Eonchemicals provided a solution with the EonTrim MS690XT product, which is specially formulated for high-speed applications like grinding, with the following features and benefits:
- Very small particle size (micro), allowing maximum penetration into the cutting area and low carry-off
- Coolant residue is friendly to the machine and helps protect the machine from rust
- Excellent tramp oil rejection, ensuring the coolant does not deteriorate quickly and has a long lifespan.
Results
After conducting a trial, the results were as follows :
Parameter | Existing | EONTRIM MS690XT |
Coolant type | Emulsion | Micro emulsion |
Surface finished | Rz: 2.0 – 2.5 | Rz: 1.4 – 2.0 |
Consumption/machine/month | 40 L | 28 L |
Tool life (dressing cycle) | 30 pcs | 60 pcs |
Machine cleanliness | dirty | clean |
Coolant life | 3 months | 12 months |
Cost Saving : | ||
a. Consumption | 30% | |
b. Dressing cycle | 100% |
From the trial data above, the improvements obtained are:
- Longer dressing cycle, increased by 2 times
- Longer coolant lifespan, from 3 months to 1 year
- Coolant consumption reduced by 30%
- Coolant waste disposal costs also automatically reduced
- Increased productivity
Conclusion
Choosing the right coolant can solve grinding wheel problems and yield the five improvements mentioned above.
Please consult with us (free of charge) for an improvement program at your company.
Consult with EON Now
We are ready to listen and provide the right chemical solution for you. Consultation with our experts is free!
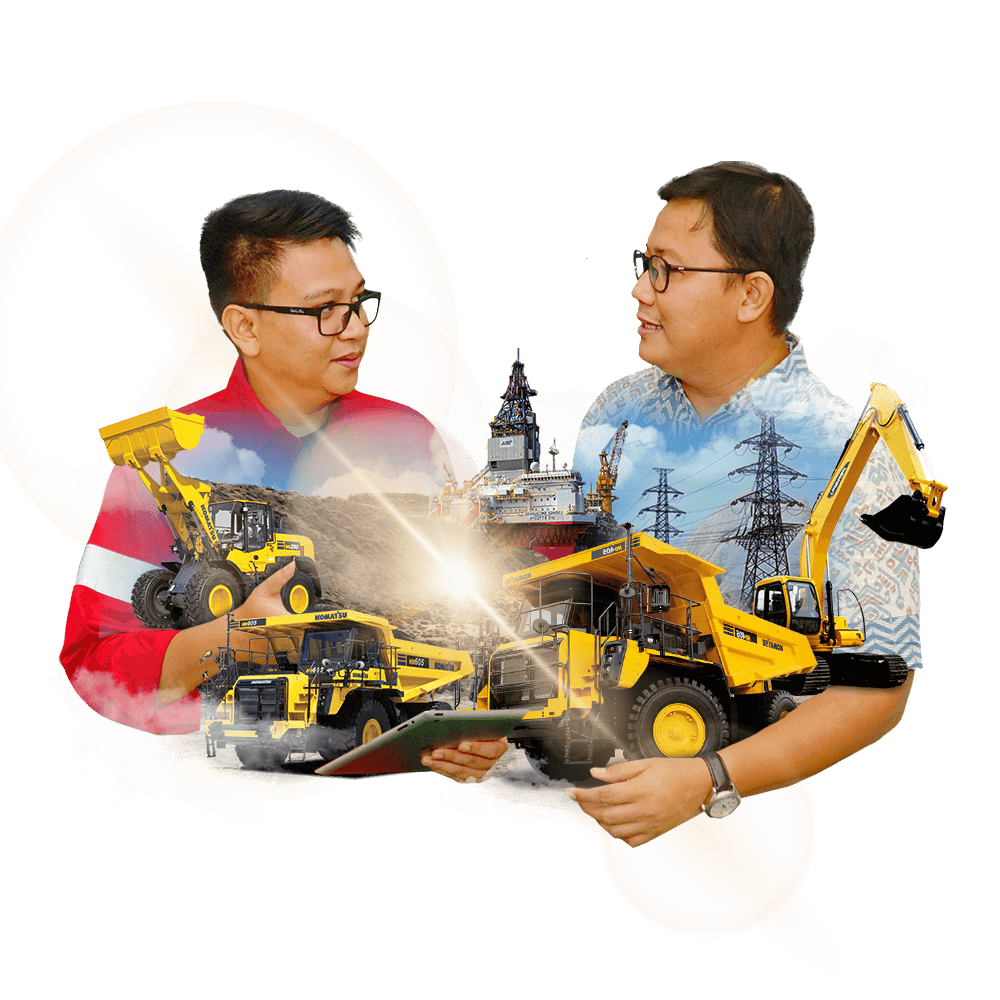