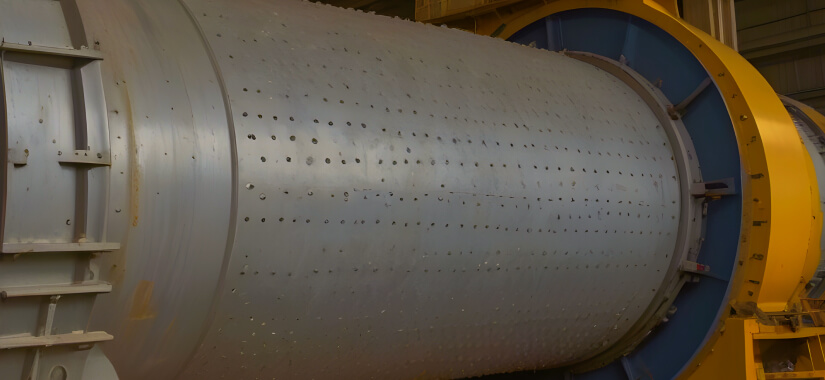
The grinding process in the cement industry is a critical stage in cement production that involves crushing cooled clinker with the addition of gypsum and other supplementary materials, such as fly ash or slag, to produce fine cement.
The grinding machine aims to reduce the particle size of the clinker to the fine powder required for cement production. Grinding is performed meticulously to ensure the appropriate particle size distribution and optimal hydration capability, which significantly affects the final quality of the cement product.
Here are some problems and solutions from Eonchemicals:
1. Problem: High Temp Grease
The grinding process in the cement industry generates a lot of heat—so much that regular grease usually can’t handle it. You’ll often see the grease start to melt, which makes it less effective and can eventually lead to faster wear and tear on the machinery.
Solution: Molykote / Dow / LE
Molykote, Dow, and Lubrication Engineers (LE) are high-temperature greases specially formulated to work at high temperatures. These products contain additives such as molybdenum disulfide (MoS2) or other additives that enhance the grease’s resistance to extreme temperatures, maintaining viscosity and lubrication stability during intensive operations.
Eonchemicals is the official distributor in Indonesia for these products, ensuring authenticity and quality. Please chat with us on WhatsApp for more information or for a free consultation regarding high-temperature lubrication programs at your site.
2. Problem: Motor Cleaner on Gear Box
The motor cleaner issue on gear boxes in the grinding process of the cement industry includes the challenge of maintaining cleanliness and optimal performance of the gear box components used in grinding raw materials like limestone and clay.
Dust and fine particles from raw materials often accumulate around the gear box, interfering with internal functions like bearings and gears. If not properly addressed, this can disrupt operations and overall product quality.
Solution: EonMotor 100
EonMotor 100 is an Eonchemicals product specially formulated to clean electric motors and dynamos from dust, oil, grease, and other buildup.
For best results, talk to our expert team about the right application dosage—so your electric motors last longer and run more efficiently. And yes, that means lower operating costs for you.
3. Problem: Road Dust
Around the grinding process in the cement industry, dust is a common issue—whether it comes from the milling activity itself or from transporting raw materials like limestone and clay.
Airborne dust can reduce visibility and traffic safety, pose health risks, and even damage equipment. And just as important, complaints from nearby communities are something that needs to be taken seriously.
Solution: DustDown 369, CSS
DustDown 339 is a dust control chemical that helps tackle dust problems by binding dust particles, keeping them from becoming airborne and spreading around.
Meanwhile, CSS (Chemical Stabilizing Solution) is used to compact and stabilize unpaved roads—helping prevent surface abrasion that often leads to dust generation.
4. Problem: Grease Quality
Low-quality grease or grease that is not suited to the application challenges will result in unsatisfactory lubrication. This is because such grease does not have the capability to adapt to challenging environments like high temperatures, high speeds, heavy loads, and significant dust.
Solution: Molykote / Dow / LE
Eonchemicals provides solutions in the form of high-quality specialty greases like Molykote, Dow, and Lubrication Engineers (LE). These greases are highly suitable and effective for lubrication systems in challenging conditions as mentioned above.
These grease products are uniquely designed to withstand high pressure, high temperatures, and high contaminants. It is crucial to maintain the optimal performance of machinery and equipment in the cement industry.
For more information or consultation about these products, please contact us.
5. Problem: Slippery and Damaged Floors
Slippery and damaged floors can certainly disrupt worker safety and operational efficiency. Slippery floors are caused by activities in the cement industry where material spills, oil, grease, and water frequently occur.
Damaged floors are caused by heavy loads operating on the floor. Problematic floor conditions (slippery and damaged) can increase the risk of workplace accidents and hinder operational activities, thus requiring appropriate solutions to address them.
Solution: EonCoat 551 / EonCoat 470
EonCoat coating products from Eonchemicals have the benefit of forming a very hard layer after curing, resistant to impact, oil, and chemicals, making them durable and non-slippery.
These specialty coating products can be used on new or old construction surfaces for maintenance.
The resulting layer provides maximum protection against harsh environmental conditions, ensuring the floor can be used safely and comfortabl.
6. Problem: Water Treatment
The focus of water treatment in this division is to treat water to become clear and free from solid contaminants that would interfere with subsequent processes. Failure in this focus can cause blockages in piping systems and equipment, reduce cooling efficiency, and increase the risk of scale and corrosion, leading to machine damage.
Solution: Coagulants and Flocculants
Eonchemicals’ solution for the above focus is to use coagulants and flocculants. Both can synergize, complementing each other in precipitating solid contaminants in the water.
Coagulants function to bind small particles into larger sizes. Meanwhile, flocculants gather the already larger particles into even larger flocs for easier sedimentation.
With the correct application of coagulant-flocculant, contaminants in the water such as limestone and clay can be precipitated more effectively and efficiently.
Contact Eonchemicals for discussion and solutions.
7. Problem: Boiler
Based on our field experience, common boiler problems include scale buildup, corrosion, and fouling. These issues are mostly caused by boiler feedwater that doesn’t meet quality standard.
Over time, they can seriously affect heat transfer efficiency, increase fuel consumption, damage equipment, and eventually drive up your operating costs.
Solution: Eon Boiler Chemicals
Eonchemicals has a range of boiler chemical formulas designed to tackle scale, corrosion, and fouling problems. Not sure which product, dosage, or application method suits your system? Just chat with one of our experts—we’re here to help.
| Read about quenching process and solutions on this site
8. Problem: Cooling Tower
A common issue we often see is the buildup of scale, rust, and algae on cooling tower surfaces. Mineral deposits and other residues from the cooling water also tend to accumulate over time.
As a result, heat transfer efficiency drops, water consumption goes up, and the whole system becomes less efficient and more wasteful.
Solution: Eon Cooling Tower Chemicals
Use EonBac GEO 9910, EonLine AG 5770, and EonScale T 2511—our specially formulated cooling tower chemicals designed to handle these problems effectively.
| Read about clinkerisation proccess problems and solutions
9. Problem: Metal Repair
Metal repair issues in the grinding unit of the cement industry often occur due to kilns and other equipment being repeatedly and constantly exposed to high temperatures. Equipment such as kilns, preheaters, and coolers are prone to significant wear and corrosion due to extreme temperature exposure and chemicals in the production process.
Damage to these metal parts can disrupt cement production, increase maintenance costs and downtime for repairs, and threaten operational safety.
Solution: Metbond 581
Metbond 581 is a compound for metal repair, rebuilding damaged metal components due to erosion and corrosion without requiring welding, thus reducing the risk in its use.
This product is suitable for various metal components such as pump bodies, impellers, propellers, grids, valves, tube sheets, water tanks, rudders, and heat exchanger components in the industry.
Metbond 581 creates a layer highly resistant to abrasion, erosion, and physical impact, making it an effective solution to extend the life and performance of critical metal components in various industrial applications.
| Also read about power plant problems and solutions
Let’s discuss grinding process problems and solutions by clicking the Whatsapp icon now.
Consult with EON Now
We are ready to listen and provide the right chemical solution for you. Consultation with our experts is free!
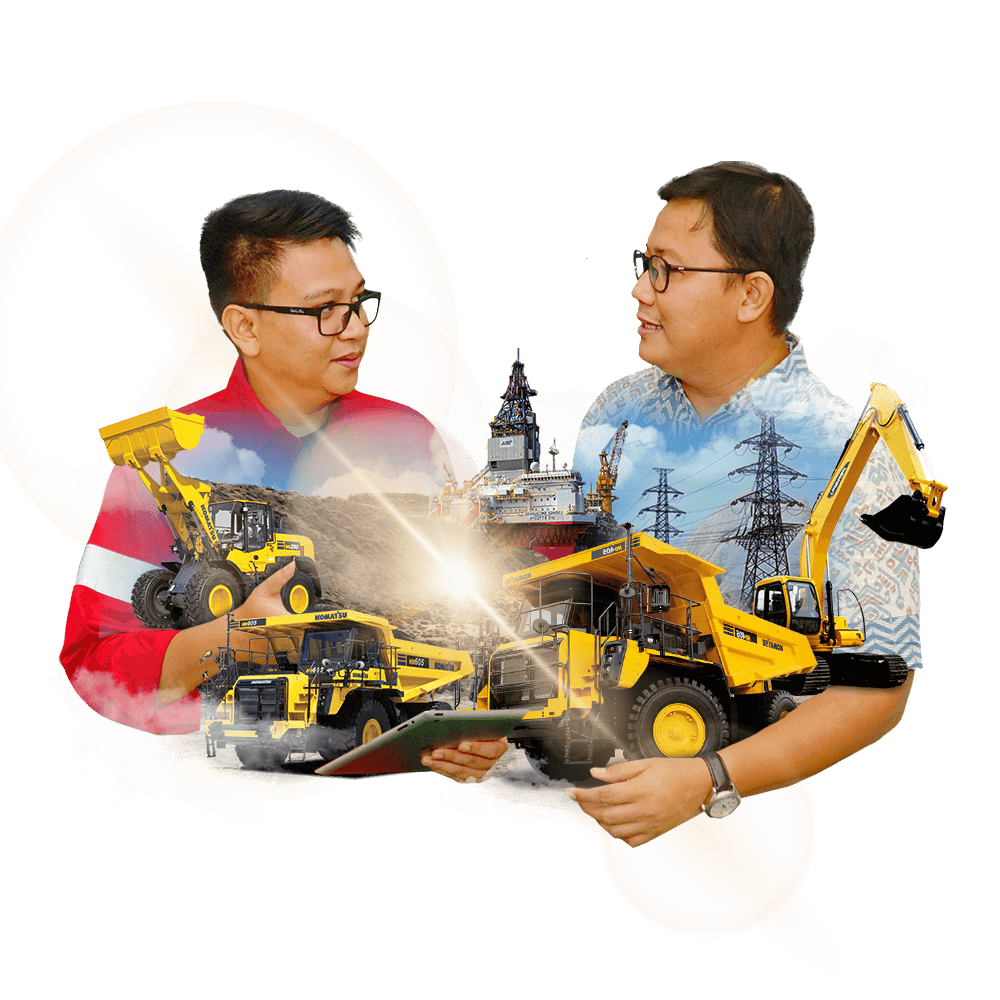