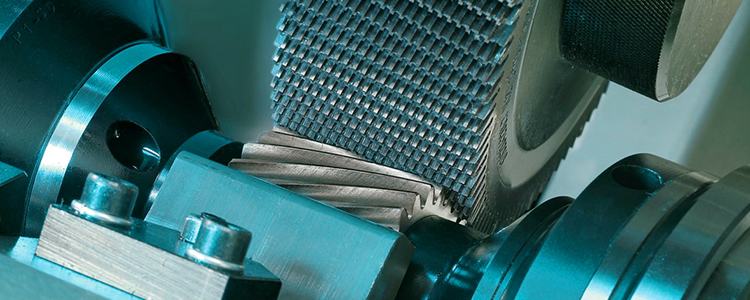
In the gear manufacturing process using shaving machines, there are often issues with kizu (fine scratches that cause parts to be rejected). One automotive company experienced kizu problems reaching up to 1,000 pieces per month. This number is excessively high and significantly detrimental to the company.
The investigation revealed the following data
- Kizu occurs in all gear shaving processes.
- The problem is caused by chips adhering to both the parts and the tools, resulting in the chips scratching the gears
As a temporary measure, the company implemented the following process changes:
- Reducing the machine speed ratio to 40%.
- Cleaning the chips from inside the machine and the coolant tank once a week
These temporary measures were somewhat successful in reducing the number of rejected gears; however, they introduced new issues, such as decreased productivity due to the reduced speed ratio and the weekly machine cleaning that required production to be halted.
From the field data, it was found that the root cause was the use of neat oil coolant without EP additives, which failed to remove chips from the cutting area. Consequently, chips adhered to the parts and tools, causing scratches on the processed gears.
Solution
To address the kizu problem, Eonchemicals introduced the EonTrim OM350C coolant, specifically formulated for gear shaving processes, with the following features and benefits:
- Contains EP additives that work under extreme load conditions to prevent chips from adhering to tools and parts.
- Produces a good surface finish.
- Low mist and evaporation, maintaining a clean work environment and controlled consumption.
- Right mixture of EP additive
Trial Results
After a one-month trial, the following results were obtained:
Parameter | Existing | EonTrim OM350C |
Surface finished | Defect rate > 10% | No Defect |
Consumption/machine/month | 80 L | 25 L |
Tool life (pcs/tool) | 1,300 | 2,400 |
Machining speed ratio | 40% | 100% |
Machine cleaning | Every 1 week | Every 2 month |
Cost-saving: | ||
a. Consumption | 68% | |
b. Tool life | 84% | |
c. Machine productivity | 150% |
Conclusion
The trial, initially aimed at addressing the kizu (product defect) issue, resulted in several improvements:
- Zero kizu.
- 68% reduction in neat oil consumption.
- 84% increase in tool life.
- 150% increase in machine productivity.
By selecting the appropriate coolant, you can address reject issues, save time, materials, and costs.
For free consultation regarding machining problems, please contact us.
Consult with EON Now
We are ready to listen and provide the right chemical solution for you. Consultation with our experts is free!
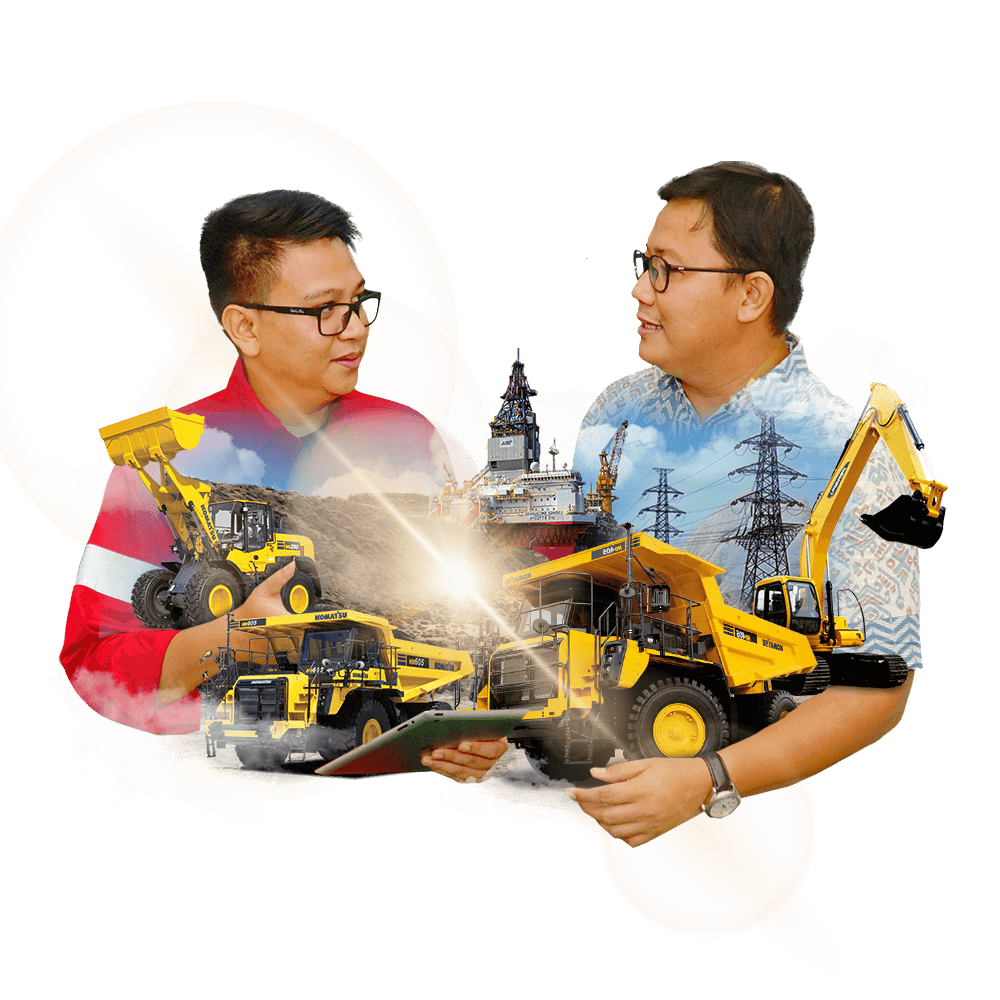