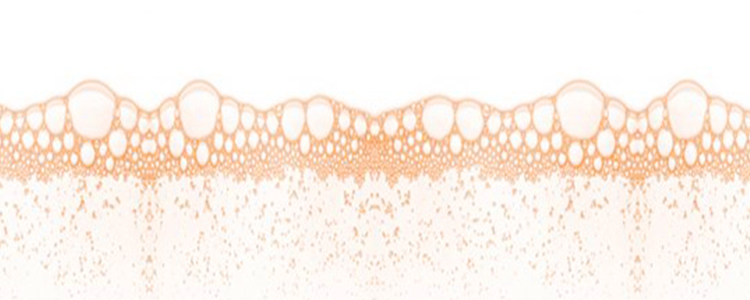
Foam or froth consists of small bubbles formed on the surface of a liquid. The presence of foam or foaming in metalworking fluids can be a serious issue. Foaming disrupts the lubrication and cooling processes. If this continues, the temperature of the cutting tool will rise and it may break.
Mechanical Foaming
There are two types of foaming: mechanical foaming and chemical foaming. Mechanical foaming is caused by processes occurring within the machine. Generally, mechanical foaming happens because the circulating metalworking fluids in the machine undergo changes in flow rate and pressure, causing the fluids to become agitated.
This change in flow rate usually occurs due to air contamination sucked into the machine’s tank. This leads to the metalworking fluids being shaken inside the hose, ultimately forming foam when recirculated back into the tank. Additionally, mechanical foaming can be caused by chips or debris from the tank being sucked into the circulation pump.
Chemical Foaming
Chemical foaming typically occurs due to one of the following:
- Incorrect concentration of metalworking fluids
- Contamination by tramp oil
- Contamination by soap
- Antifoam in the metalworking fluids not functioning
To accurately determine the cause of chemical foaming, it is best to check it first in a lab.
Determining the Type of Foaming in Metalworking Fluids
- Take a sample of the metalworking fluids from the tank into a bottle (half-filled)
- Shake the bottle for 15-30 seconds
- Observe the foaming
- If the foam disappears within less than 30 seconds, it is mechanical foaming
- If the foam does not disappear in 30 seconds or more, it is chemical foaming.
Solutions
Addressing Mechanical Foaming
- Use Antifoam or Defoamer as a first aid measure
- Maintain the volume of metalworking fluids in the machine to prevent it from being too low
- Perform regular filtration and draining to prevent chip buildup
Addressing Chemical Foaming
- Use Antifoam or Defoamer as a first aid measure
- Check the foaming coolant sample in the lab to determine the cause
- Adjust the concentration based on recommendations
- When contaminants in the coolant are high, it is advisable to drain the system
If you have foaming issues with metalworking fluids, please contact us for consultation and solutions.
Consult with EON Now
We are ready to listen and provide the right chemical solution for you. Consultation with our experts is free!
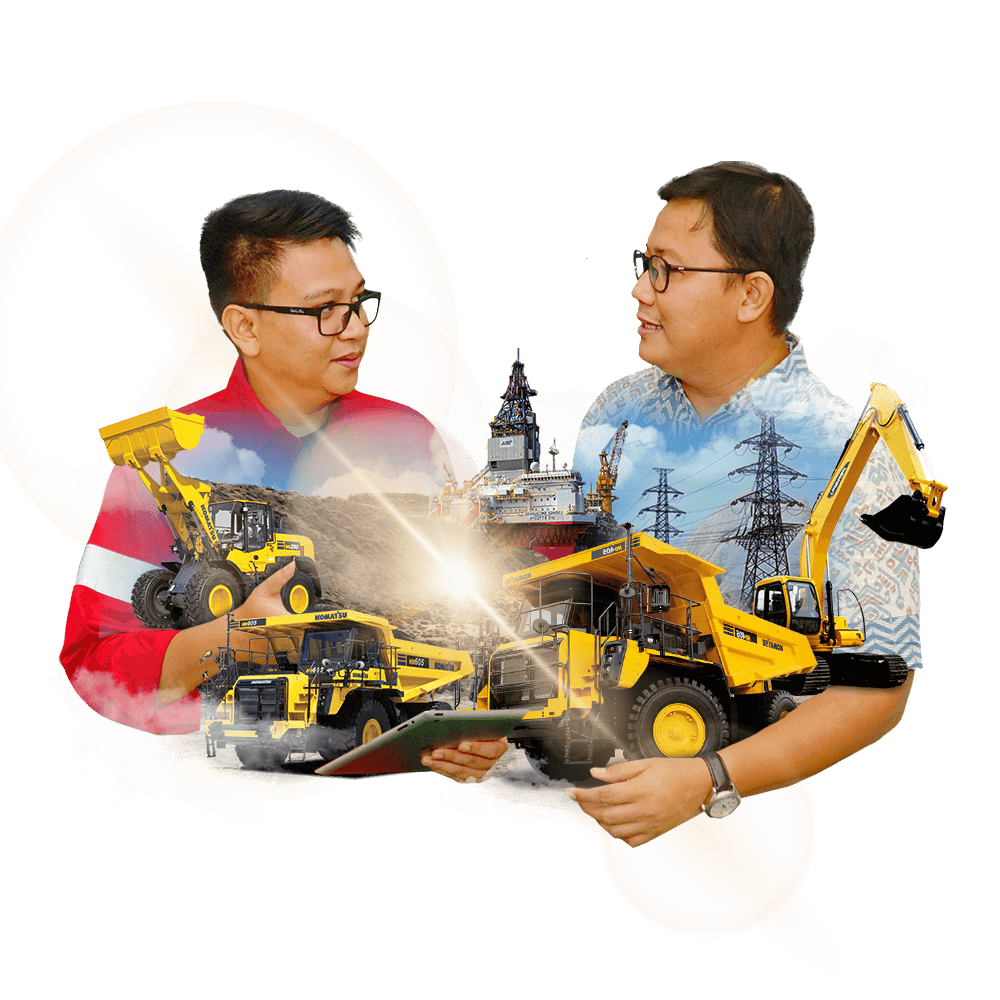