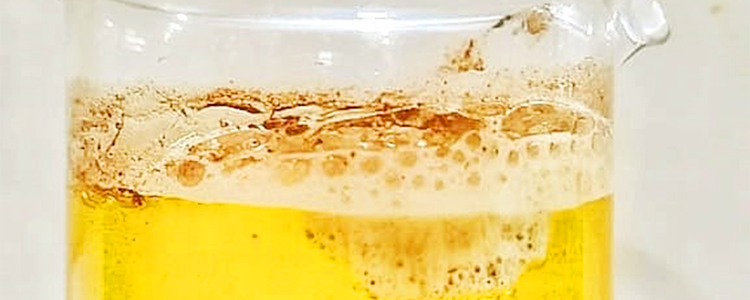
The primary goal of the oil & gas industry is to produce as much crude oil as possible and as quickly as possible with the available facilities in the field. Despite meticulous planning and support from reliable production facilities, problems sometimes arise. One issue that can significantly impact the production process is foaming.
Foaming Process and Its Issue
Foam can form when gas dissolved in a liquid or solid phase creates bubbles that do not burst due to high surface tension. Gas can dissolve through agitation or mechanical activities. Crude oil containing natural surfactants such as resins, asphaltenes, and naphthenic acids can cause stable foaming. Additionally, the viscosity of crude oil can also lead to foaming.
The presence of foam in crude oil disrupts the performance of equipment such as separators and amine-glycol systems.
Foaming disrupts the performance of oil & gas industry equipment
Foam in separators causes fluid turbulence, disrupting the separation process of water and oil. Foam can also cause crude oil carry-over into the gas phase, thereby reducing crude oil production.
The disruption in the separation of water and oil results in lower oil quality due to emulsions and inaccurate instrument readings. If this issue is left unaddressed, losses will continue to increase.
Solution
The foaming issue can be resolved with chemical anti-foam agents or defoamers, which function to break down already formed foam. The working principle of defoamers is to replace the surfactant on the foam surface formed between the dissolved gas and the liquid, causing the gas to be released from the foam and the foaming liquid to merge with other liquids. When the gas is released from the liquid phase, foaming no longer occurs.
Defoamer usage results
Success Story
One oil & gas company faced foaming issues while loading crude oil via truck. This made it difficult for them to measure the volume of crude oil being delivered. They usually required a long time to read the crude oil level.
Eonchemicals provided a solution by injecting the chemical EonAntifoam P233. In field applications, the time needed to break down the foam was less than 1 minute.
The successful use of EonAntifoam P233 to solve the level reading issue significantly saved reading time.
For further consultation on foaming problems, please contact us.
Consult with EON Now
We are ready to listen and provide the right chemical solution for you. Consultation with our experts is free!
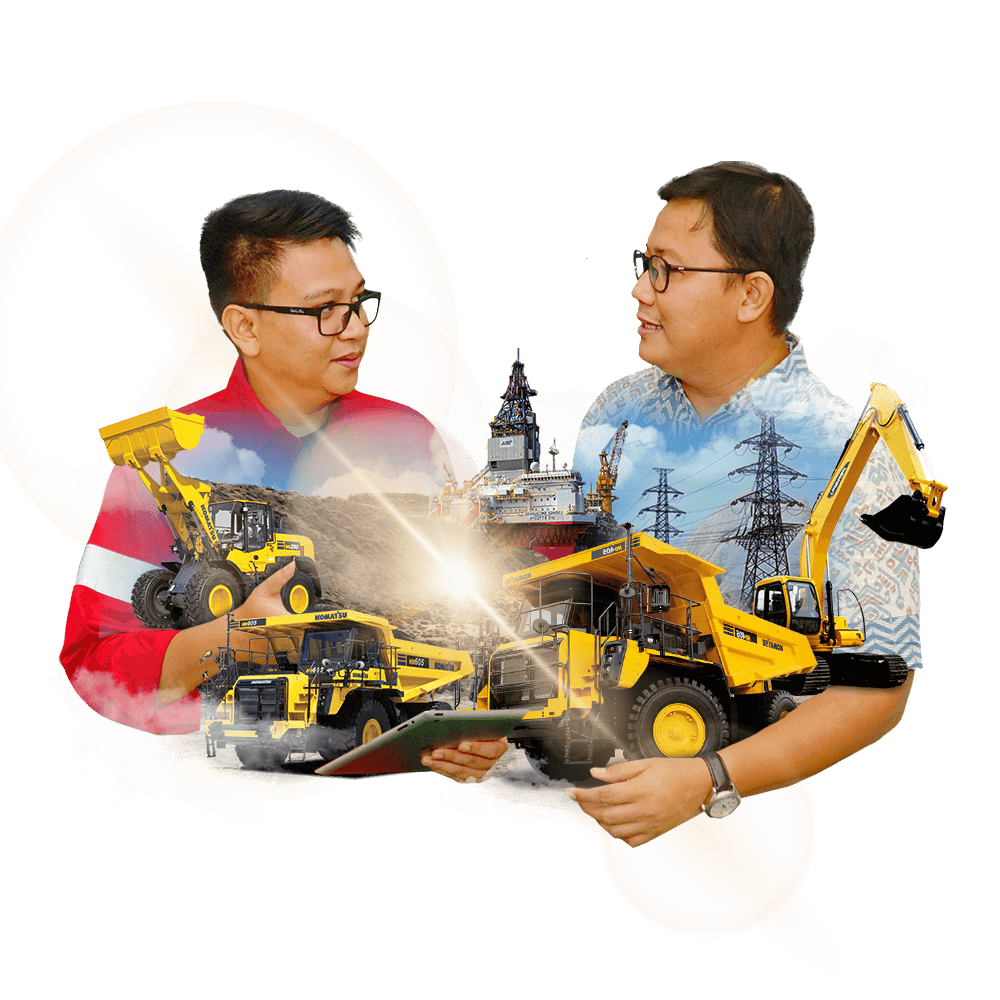