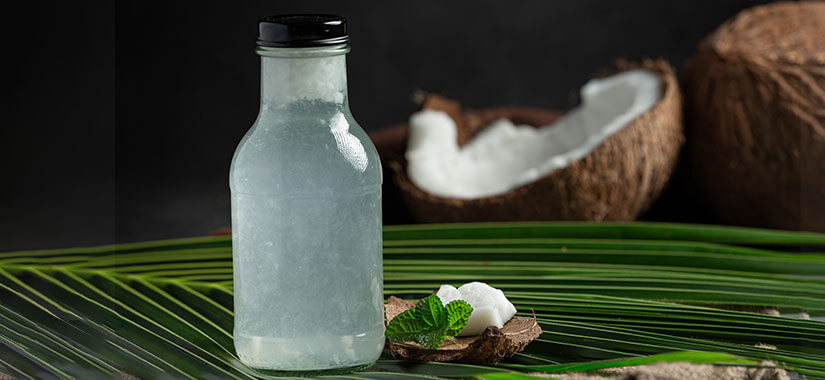
The filling unit in the food industry, particularly for coconut water products, refers to the process of filling the product into its final packaging, such as bottles, cans, or other containers. This process is carried out after the coconut water has undergone various processing stages like filtration, pasteurization, and sterilization to ensure its safety and quality.
Filling is done using automated equipment designed to precisely measure and fill the correct amount of coconut water into each package, and to seal the packaging tightly to maintain freshness and prevent contamination.
Please contact us, Eonchemicals, for effective and innovative solutions to any problems you might encounter, such as those listed below:
1. Problem: Long CIP Cycle Time
A long CIP (Cleaning In Place) cycle time in the filling process for coconut water can affect overall production efficiency. The CIP process is crucial for ensuring the cleanliness of filling equipment without disassembly.
A long CIP cycle time can reduce production capacity, increase energy consumption, and incur additional costs.
Solution: Eon CIP
Eon CIP is the right solution to address the issue of long CIP cycle times in the filling process for coconut water in the food industry due to its effective formula that thoroughly and quickly cleans the equipment.
Eon CIP comes in several variants, each with unique features. This product is certified by the National Sanitation Foundation (NSF) to ensure its quality meets regulations and is halal-certified by the Indonesian Ulema Council (MUI) to enhance consumer confidence.
Please chat with us on WhatsApp to learn more about the variants and other details.
2. Problem: Microbiological Contamination
In the food industry, microbiological contamination in the filling process for coconut water is a serious issue that can threaten the safety and quality of the product. Contamination by microorganisms such as bacteria, fungi, or yeast can occur if adequate sterilization or sanitation is not performed on the filling equipment and environment.
Microbiological contamination can make coconut water unsafe for consumption, reduce its shelf life, and pose a health risk to consumers if not detected and handled properly.
Solution: Eon Sanitizing
This product is the right solution for the problem of microbiological contamination in the coconut water filling process in the food industry due to its effective formula in killing various types of pathogenic microorganisms, including bacteria, fungi, and yeast.
For the correct use of this solution product, please contact us, Eonchemicals. Create a safe filling process, reduce the risk of microbiological contamination, and comply with hygiene standards and food safety regulations.
3. Problem: Contaminated Bottles
The problem of contaminated bottles in the coconut water filling process is a situation that can threaten the cleanliness and safety of the final product. Contaminants in bottles can come from various sources, such as residues from previous cleaning processes, airborne particles, or cross-contamination with other materials in the filling area.
Contaminants entering the coconut water bottles can reduce product quality, increase health risks to consumers, and lead to product recalls from the market, damaging brand reputation and trust.
Solution: Eon WashBrite 330
Eon WashBrite 330 can be a solution for the problem of contaminated bottles in the coconut water filling process in the food industry. This solution product is a cleaning liquid specially formulated from selected alkalis and unique surfactants, providing excellent cleaning power with low foaming.
This product is very suitable for cleaning polycarbonate bottles in the food and beverage industry. Please discuss with us, click the WA button for additional insights.
4. Problem: Stains/Scale on Equipment
Another problem is stains or scale on the filling equipment for coconut water. Stains or scale can form due to mineral or organic residues adhering to the equipment surfaces after repeated use.
This problem not only reduces the visual cleanliness of the equipment but can also affect the quality of the final product if not addressed properly. Additionally, poorly removed stains or scale can result in non-compliance with the expected hygiene and food safety standards in the food industry.
Solution: EonBright 353
This product is a special cleaner formulated to tackle stains/scale. EonBright 353 can be used on various types of equipment materials, ensuring that no residues remain that could affect the quality or cleanliness of the final product.
Please consult with us about this solution product. By using EonBright 353 regularly, you can maintain the cleanliness of the filling equipment, reduce the risk of cross-contamination between productions, and ensure compliance with the strict hygiene and food safety standards regulated in the food industry.
5. Problem: Short Regreasing Interval
The issue of a short regreasing interval in the coconut water filling process needs to be a primary concern, as it can lead to increased grease procurement costs, as well as more labor and time requirements.
A short regreasing interval indicates that the lubricant on machine components, such as bearings or filling mechanisms, degrades quickly or cannot withstand operational conditions.
Find a solution to this problem with Eonchemicals.
Solution: LE Lubricant
LE Lubricant can be a solution for the problem of short regreasing intervals in the coconut water filling process in the food industry due to its specially designed formula to provide long-lasting and effective lubrication.
This product contains special additives that enhance thermal stability (heat resistance) and pressure resistance, reducing excessive friction on machine components such as bearings or filling mechanisms. Therefore, by using LE Lubricant, you can extend the interval between regreasing, reduce the frequency of required maintenance, and increase the lifespan of machine components.
Eonchemicals is the official agent of Lubrication Engineers (LE) in Indonesia. With us, you are guaranteed to get original products with genuine quality and adequate technical service.
6. Problem: Grease/Oil on Chains Contaminating Products
Inadequate quality grease or oil will cause this problem. Product contamination in the coconut water filling process is a serious concern as it can threaten the safety and quality of the final product.
Such contamination can also lead to product recalls from the market, additional costs for testing and quality control, and damage the company’s reputation in the highly regulated and food safety-sensitive food industry.
Solution: Molykote AFC
Specialty lubricant Molykote AFC is the right solution to address the problem of grease or oil contaminating products in the coconut water filling process in the food industry due to its specially designed formula for applications in sensitive food and beverage environments.
This product has heat-resistant properties and is resistant to cleaning fluids used in machine sanitation processes, making it less likely to wash away and transfer to the final product. Molykote AFC (Anti Friction Coating) also provides stable and non-toxic lubrication, and has the ability to reduce friction and wear on chains or filling mechanisms, ensuring no contamination is transferred to the filled coconut water.
To obtain genuine Molykote products, please contact us, Eonchemicals, as the official distributor of Molykote Indonesia. With us, you not only get quality assurance due to its authenticity but also satisfying technical service.
7. Problem: Falling Bottles on Conveyor
Another common problem is bottles falling on the conveyor during the coconut water filling process. This problem needs to be a primary concern as it can result in bottle damage, product waste, and potential cross-contamination in the production environment.
Falling bottles can cause cracks or breaks, potentially spreading glass or plastic shards into the processing area, threatening the safety and quality of other products. Additionally, such incidents can disrupt the overall production flow, cause delays in the filling process, and increase the risk of workplace accidents.
Solution: EonDrylube 805
EonDrylube 805 is an emulsion-based dry lubricant specifically formulated for application on modular conveyors. This lubricant is highly effective for use on conveyors to minimize friction, thereby reducing the risk of bottles falling while on the conveyor.
| Read also the problem of filling coconut milk in the food industry
Moreover, this product is NSF H1 certified for dry lubricants and Halal MUI certified, ensuring its safety for use in the food and beverage industry. Suitable for various types of conveyors such as plastic, stainless steel, can transfer, in-floor chain, and mixed belt.
Please consult with us for its application.
Consult with EON Now
We are ready to listen and provide the right chemical solution for you. Consultation with our experts is free!
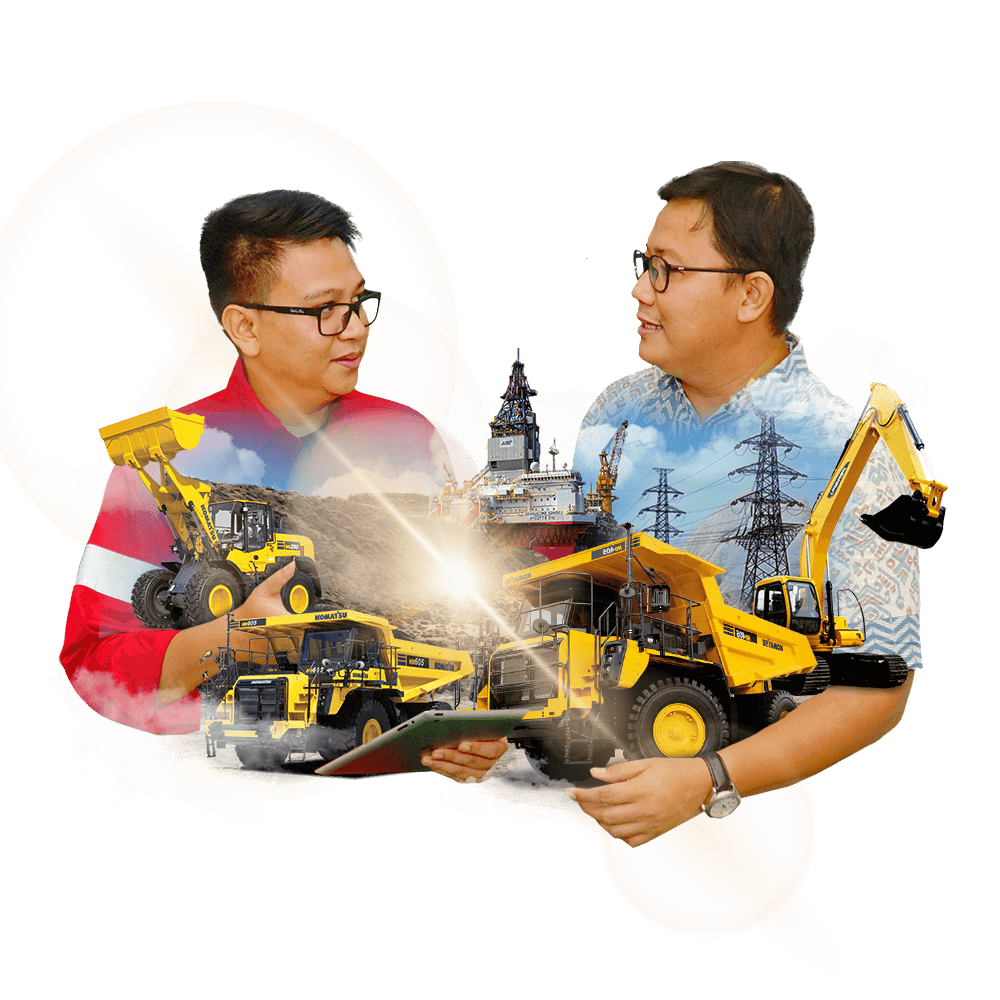