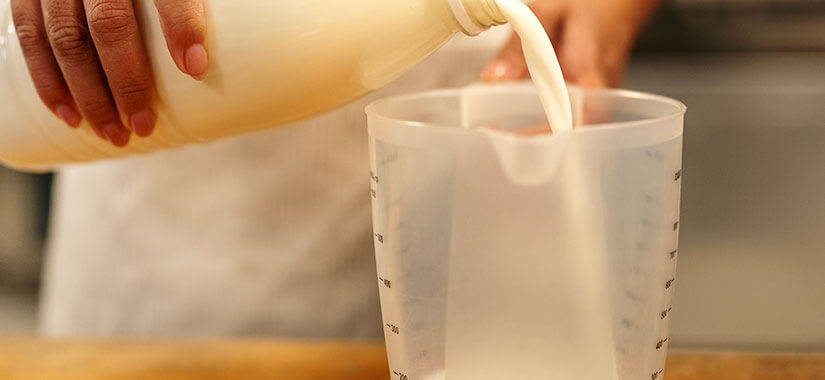
The filling process in coconut milk production is a critical stage where the processed coconut milk is placed into its final packaging, such as bottles, cans, or cartons. Efficiency and precision in the filling process are essential to meet industry standards and maintain consumer satisfaction.
Common problems and solutions from Eonchemicals include:
1. Problem: Long CIP Cycle Time
A long CIP (Cleaning in Place) cycle time in the filling process of coconut milk production can result in significant downtime, reducing operational efficiency and increasing production costs.
This problem arises because the filling process requires thorough cleaning. However, if the CIP cycle time is too long, production will halt for an extended period, leading to higher losses due to downtime.
Solution: Eon CIP
Eon CIP (Cleaning in Place) is the perfect solution to address the long CIP cycle time issue in the coconut milk filling process, thanks to its effective formula that cleans equipment thoroughly and quickly.
Eon CIP comes in various series, each for a specific purpose. This product has received certification from the National Sanitation Foundation (NSF) to ensure its quality complies with regulations and is halal-certified by MUI to enhance consumer trust.
Please chat with us on WhatsApp for details on the variants and other information.
2. Problem: Microbiological Contamination
Microbiological contamination in the coconut milk filling process is a serious issue that can threaten the safety and quality of the final product. This contamination can occur if the filling equipment is not properly cleaned and sanitized.
Therefore, creating a sterile filling environment and hygienic equipment is crucial.
Please contact Eonchemicals for Eon Sanitizing application to resolve this issue.
Solution: Eon Sanitizing
Eon Sanitizing is an effective solution for addressing microbiological contamination in the coconut milk filling process in the food and beverage industry. This product is formulated to thoroughly sterilize equipment and surfaces, eliminating pathogenic microorganisms that can cause contamination.
With a strong yet safe formulation, Eon Sanitizing helps clean nozzles, pipes, tanks, and other filling areas from harmful microorganisms. Regular use of Eon Sanitizing significantly contributes to producing safe and high-quality coconut milk, complying with food safety standards.
Please contact Eonchemicals for the application of Eon Sanitizing to address this issue.
3. Problem: Bottles Containing Contaminants
Bottles containing contaminants in the coconut milk filling process can affect the quality and safety of the final product. Contaminants can come from various sources, including residues from previous production processes, dust particles, microorganisms, or chemicals that accidentally enter during bottle storage or handling.
The presence of these contaminants can cause product damage, taste alteration, nutritional value reduction, and potential health risks for consumers. Therefore, ensuring that bottles used in the filling process are clean and free from contaminants is crucial to maintaining the quality of coconut milk and meeting strict sanitation standards in the food industry.
Solution: Eon WashBrite 330
This solution product is a specially formulated liquid from selected alkalis and unique surfactants, providing excellent cleaning power and low foaming levels. This product is ideal for cleaning polycarbonate bottles in the food and beverage industry.
Thanks to its special alkali and surfactant formulation, Eon WashBrite 330 can quickly remove dirt and has good rinsing power. Its low-foaming surfactants are suitable for use in both soft and hard water areas. This product is compatible with plastics and rubber commonly used in the food and beverage processing industry, but caution is needed when used on aluminum and zinc as they can corrode.
4. Problem: Stains/Scale on Equipment
Stains or scale on equipment in the filling process for products like coconut milk in the food industry is a common challenge that can disrupt production. These stains and scales can form due to product residues adhering to equipment surfaces, especially in hard-to-reach areas such as corners and folds of filling equipment.
The accumulation of stains and scale not only reduces operational efficiency by slowing down the process but also diminishes the cleanliness of the final product and increases the risk of contamination
Please consult us for the use of EonBright 353 as a solution.
Solution: EonBright 353
This product is a cleaner, brightener, descaler, and pickling agent formulated to clean stains/scale and brighten the surface of stainless steel materials.
It is not overly corrosive and is safe for all types of metals, also functioning as a rust remover. Please chat with us by clicking the WA icon button for further consultation.
5. Problem: Short Regreasing Period
A short regreasing period on filling equipment for products like coconut milk in the food industry is a common issue. This can be caused by heavy operational conditions and continuous equipment use, as well as the selection of inappropriate grease types.
This issue can disrupt production by requiring more frequent maintenance and grease replacement, potentially increasing operational costs and machine downtime
Solution: LE Lubricant
LE Lubricant is an effective solution to address the short regreasing period issue on filling equipment for products like coconut milk. This lubricant product has a strong formula to provide longer-lasting and effective lubrication, thereby extending the regreasing period.
By using LE Lubricant, you save time, costs, and effort as the regreasing period becomes longer. Please contact us for consultation
6. Problem: Grease/Oil on Chains Contaminating Products
Grease or oil contaminating products in the filling process for products like coconut milk is a common problem.
This contamination usually occurs due to errors in selecting the type of lubricant. Ordinary types of lubricants tend to drip and become contaminants. The most appropriate solution is to use dry lubricants, such as AFC (Anti Friction Coating).
Solution: Molykote AFC
Molykote AFC (Anti Friction Coating) is an effective solution to address the product contamination issue due to dripping grease or oil on chains. This is because AFC is a dry lubricant, so it does not drip as you might worry.
This product is designed with special technology that provides high and long-lasting lubrication on equipment chains, reducing the possibility of product contamination as it does not drip.
Eonchemicals is the official distributor of Molykote Indonesia, ensuring you get the original product with the same quality. Through an official distributor, you will also receive good technical service.
7. Problem: Bottles Falling on the Conveyor
Bottles falling on the conveyor during the filling process for products like coconut milk is a common situation that can disrupt operational smoothness.
Falling bottles can cause damage to the product, the bottle itself, or even other surrounding equipment. Additionally, leaks or spills that may occur due to falling bottles can lead to product wastage and affect the efficiency of the filling process.
| Visit the coconut milk packaging problems and solutions page
Solution: EonDrylube 805
This type of dry lubricant emulsion-based product is specially formulated for conveyor applications. EonDrylube 805 provides highly effective lubrication on conveyors to minimize friction, thereby reducing the risk of bottles falling.
| Read coconut water filling problems and solutions
As a dry lubricant, EonDrylube 805 has NSF H1 certification and halal certification from MUI. These certifications prove its safety for applications in the food and beverage industry and enhance public trust.
For the application of EonDrylube 805 at your place, please contact us.
Consult with EON Now
We are ready to listen and provide the right chemical solution for you. Consultation with our experts is free!
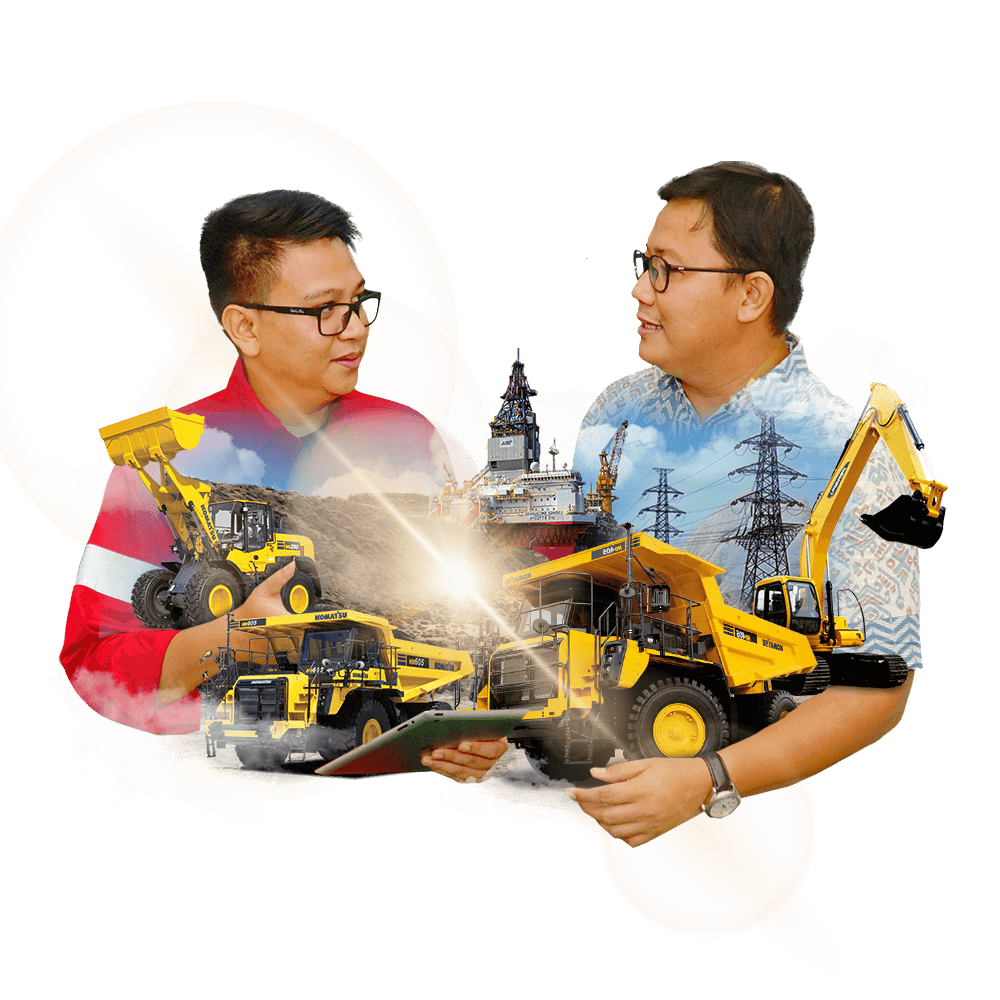