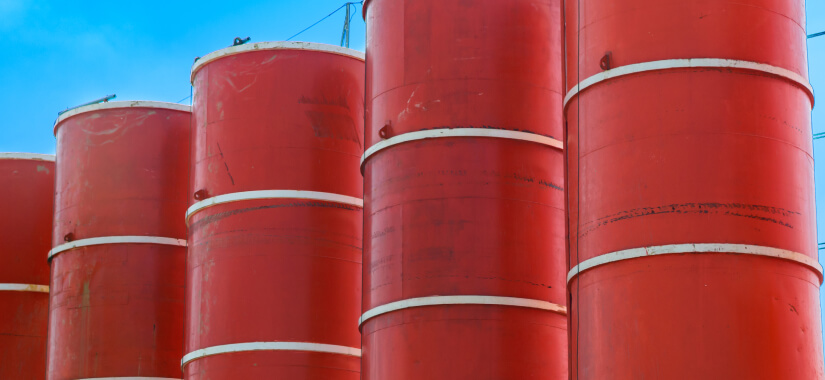
A depot station in the oil and gas industry is a facility used for the storage, processing, and distribution of oil and gas products. This depot serves as a connecting point between field production and distribution to end-users or further processing facilities.
Typically, a depot station is equipped with large storage tanks, pumps, piping systems, and safety and monitoring equipment to handle oil and gas products safely and efficiently.
Here are some common problems that occur in this unit along with their solutions from Eonchemicals
1. Problem: Oil Spills
Oil spills at an oil depot station are a critical issue that can occur during the storage, loading, or unloading of oil and other petroleum products. These spills can be caused by tank leaks, equipment failures, or operational errors.
The impacts include soil and water contamination, which can damage local ecosystems and threaten human health. Furthermore, oil spills at a depot station can lead to fires or explosions, resulting in significant financial losses, including repair costs and regulatory fines.
Solution: EonSpill 500, Absorbent Series
EonSpill 500 is a powerful and effective oil spill dispersant (OSD) designed to disperse and maintain the dispersion of oil in both freshwater and seawater. This product is formulated to minimize environmental impact due to its very low toxicity.
It is highly effective for various types of oil spills, thereby reducing the risk of environmental damage and facilitating the cleanup process. Due to its environmentally friendly nature and high efficiency, EonSpill 500 is a reliable solution for addressing oil spills in various water conditions.
Absorbent is a solution product for dealing with oil spills on floors (land). It is an effective kit for cleaning spills and maintaining the cleanliness and safety of the work area. Eonchemicals provides various types of absorbents that can be selected according to the specific needs of your industrial field.
Want to get the most suitable solution for your needs? Please consult our team via WhatsApp now!
2. Problem: Fire
Fire at an oil and gas depot station is a very serious risk due to the flammable nature of oil and gas products. Fires can occur due to fuel leaks, sparks from electrical equipment, or equipment failures.
The impacts can be highly destructive, including threats to worker safety, severe damage to infrastructure, and the potential for explosions. Additionally, fires at a depot station can cause air pollution and significant financial losses due to repair, cleanup costs, and operational shutdowns
Solution: FireShield 700
FireShield 700 is a water-based foam-forming chemical specifically formulated as a fire-fighting foam concentrate. This product has received UL certification. It is applied at a proportion of only 3% to water (3 parts FireShield 700 and 97 parts water).
It is highly effective in extinguishing hydrocarbon fires such as gasoline, kerosene, diesel, and others. With its superior fire-extinguishing capability, this product is a reliable choice for protecting industrial environments and other areas at high risk of hydrocarbon fuel fires.
3. Problem: Hard-to-Open Bolts Due to Rust
The issue of hard-to-open bolts due to rust at a depot station is common due to the harsh environment and frequent exposure to high humidity and extreme weather conditions. Rust can make bolts and nuts difficult to open, which can impede necessary maintenance, repairs, or equipment replacement.
This can cause delays in operations or even further damage if bolts cannot be safely opened. A special lubricant is required for the solution.
Solution: Molykote 1000
Molykote 1000 is a thread paste designed to facilitate the release of bolts. This specialty lubricant product provides optimal lubrication on bolt threads, reducing friction and preventing corrosion, so bolts can be easily removed even after long-term use.
Molykote 1000 is highly suitable for industrial applications where efficiency and ease of maintenance are crucial.
4. Problem: Peeling Tank Paint
When paint peels, the metal surface becomes exposed and vulnerable to corrosion, which can accelerate material degradation and potentially cause leaks or structural damage to the tank.
The impact is not only limited to physical damage but also includes potential environmental contamination if leaks occur from inadequately protected tanks.
Common causes of peeling paint include improper application, poor surface preparation before painting, or the use of paint unsuitable for specific environmental conditions.
Solution: EonCoat 551/470
EonCoat 551 is an alkaline-resistant external coating, a protective external paint with high alkaline resistance. This product is an epoxy coating designed to provide maximum protection against corrosion, dirt, and chemical spills.
EonCoat 470 is a permanent heavy-duty protective coating. This coating solution product is designed to dry quickly, withstand water, and prevent the rusting process. It is highly suitable for protecting tanks, pipes, iron structures, and other substrates.
| Read also oil & gas industry refinery problems and solutions
To get recommendations for the type of coating that suits your needs, please contact our coating experts.
Consult with EON Now
We are ready to listen and provide the right chemical solution for you. Consultation with our experts is free!
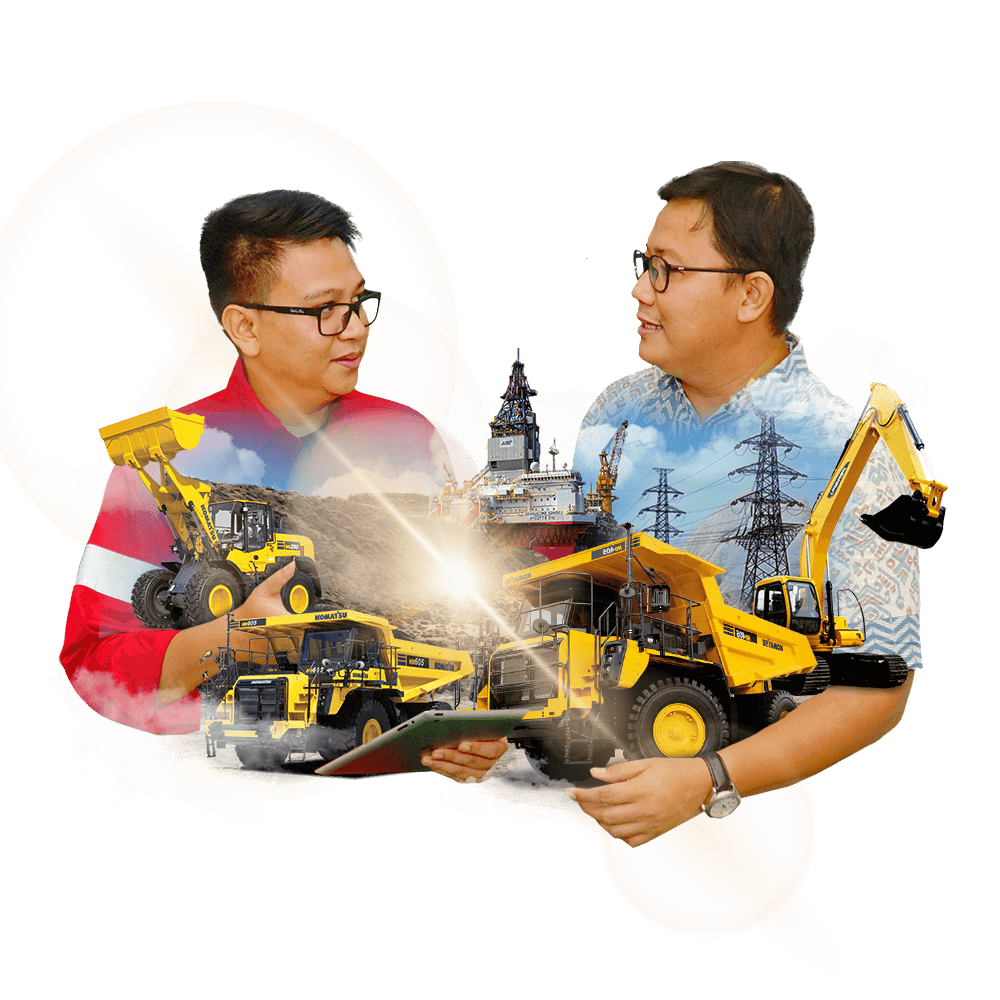