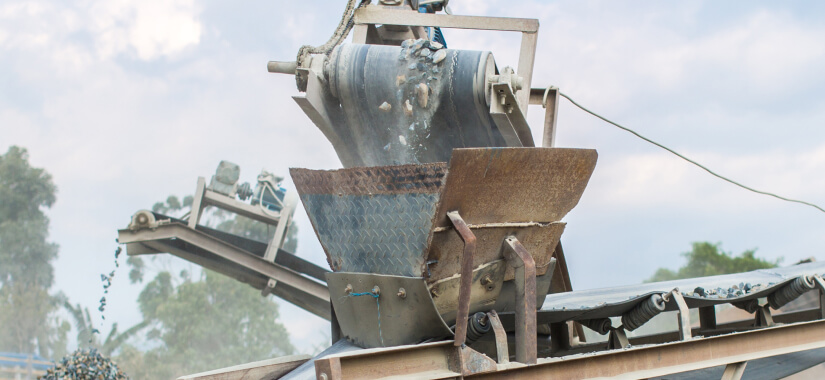
A cone crusher is a crushing tool used in the mineral mining industry to reduce the size of rocks by compressing the material between a rotating cone and a stationary wall. This equipment is capable of handling rocks with high hardness, producing uniformly sized particles, and being energy-efficient.
Several common problems with cone crushers and solutions from Eonchemicals are as follows:
1. Problem: High Load, Low Speed, and Dusty Environment
Cone crushers handle heavy loads, which results in low operational speed. A dusty environment can further degrade the performance of the cone crusher. Wear and tear can occur more rapidly, necessitating higher maintenance costs and increasing the potential for damage to critical components.
The combination of high load, low speed, and a dusty environment is a serious issue that requires an appropriate solution.
Solution: Molykote Long Term 2 Plus
This specialty lubricant is ideal for addressing the aforementioned cone crusher issues because:
- It can operate under high loads.
- It has excellent resistance to water and dust.
- Its high stability ensures that the lubricant does not easily melt, resulting in cost savings due to longer re-lubrication intervals.
- It provides maximum protection between metal surfaces.
- It offers reliable anti-corrosion protection.
- With an NLGI 2 standard, this lubricant is suitable for various industrial applications requiring effective and long-lasting lubrication.
For further consultation on industrial lubrication, please contact our expert team. Eonchemicals is ready to help you find the best lubrication solution for your industrial needs.
2. Problem: Rusty Bolts, Difficult to Remove
In cone crushers, rusty bolts are often encountered, making them difficult to remove. The harsh working environment, with exposure to dust, moisture, and chemicals, accelerates bolt corrosion.
When these bolts rust, removing them becomes very challenging, hindering routine maintenance and repair processes. This problem inevitably prolongs downtime, reduces efficiency, and increases operational costs.
To address this issue, Eonchemicals offers a comprehensive solution program as follows:
Molykote P40
This product is a paste lubricant recommended to prevent rusty bolt problems. Molykote P40 is highly reliable for various assembly and continuous lubrication tasks in corrosive environments such as areas with high humidity or water splashes. Its features and benefits include:
- Corrosion protection
- Strong adhesion
- Water resistance
- Excellent anti-fretting properties
Molykote GN Plus
This specialty lubricant also functions similarly to Molykote P40, preventing rusty bolts from becoming difficult to remove. Molykote GN Plus is a solid lubricant paste for assembling and operating metal components, including bolt installation. Its features and benefits include:
This product is effective in preventing corrosion caused by friction and scratches and has excellent anti-corrosion properties. By reducing fretting corrosion formation, this product facilitates disassembly, making it more efficient and practical.
Additionally, it has high load-bearing capacity and low friction coefficient, providing optimal protection against stick-slip. These qualities ensure that components remain protected and function well under various operating conditions.
For further information or a free consultation, please contact us.
EonPen 100
If the above two solutions are intended to prevent problems, EonPen 100 is used when the issue of rusty bolts that are difficult to remove has already occurred.
EonPen 100 is a penetrating fluid, a chemical that can penetrate, lubricate, and break down adhered rust. This product is the best solution for disassembling rusty bolts that are difficult to remove. Its other advantages include:
- Usable for electrical equipment and machinery
- Pleasant aroma, not pungent
Please contact our team for more information via WhatsApp chat.
3. Problem: Lubricant Dries Quickly
A lubricant that dries quickly can adversely affect machinery or equipment because it fails to provide adequate protection against friction and heat generated during operation. This can cause components like bearings, pistons, and gears to wear out more rapidly. Additionally, a lubricant that dries quickly requires more frequent re-lubrication, making it inefficient and wasteful.
To address this issue, we offer an effective and long-lasting solution with the specialty lubricant below.
Solution: Molykote Long Term 2 Plus
Molykote Long Term 2 Plus is a special grease designed to handle heavy loads, ideal for long-term lubrication applications. This grease excels in providing reliable and durable protection under various industrial operating conditions.
4. Problem: Abrasive and Rapid Wear Due to Transfer Points and Chutes
This issue can lead to reduced equipment lifespan and more frequent maintenance requirements, thereby decreasing overall operational efficiency.
| Open page about jaw crusher problems and solutions
Solution: Metbond 782
MetBond 782 is a two-component ceramic epoxy that functions as a coating. This product is ideal for application on vertical and overhead surfaces without the risk of dripping. Its application process is straightforward, starting with cleaning the surface, then mixing parts A and B of the epoxy in a 4:1 ratio until evenly mixed.
| Read also tertiary crusher problems and solutions
Discuss your cone crusher problems to get the solution from us.
Consult with EON Now
We are ready to listen and provide the right chemical solution for you. Consultation with our experts is free!
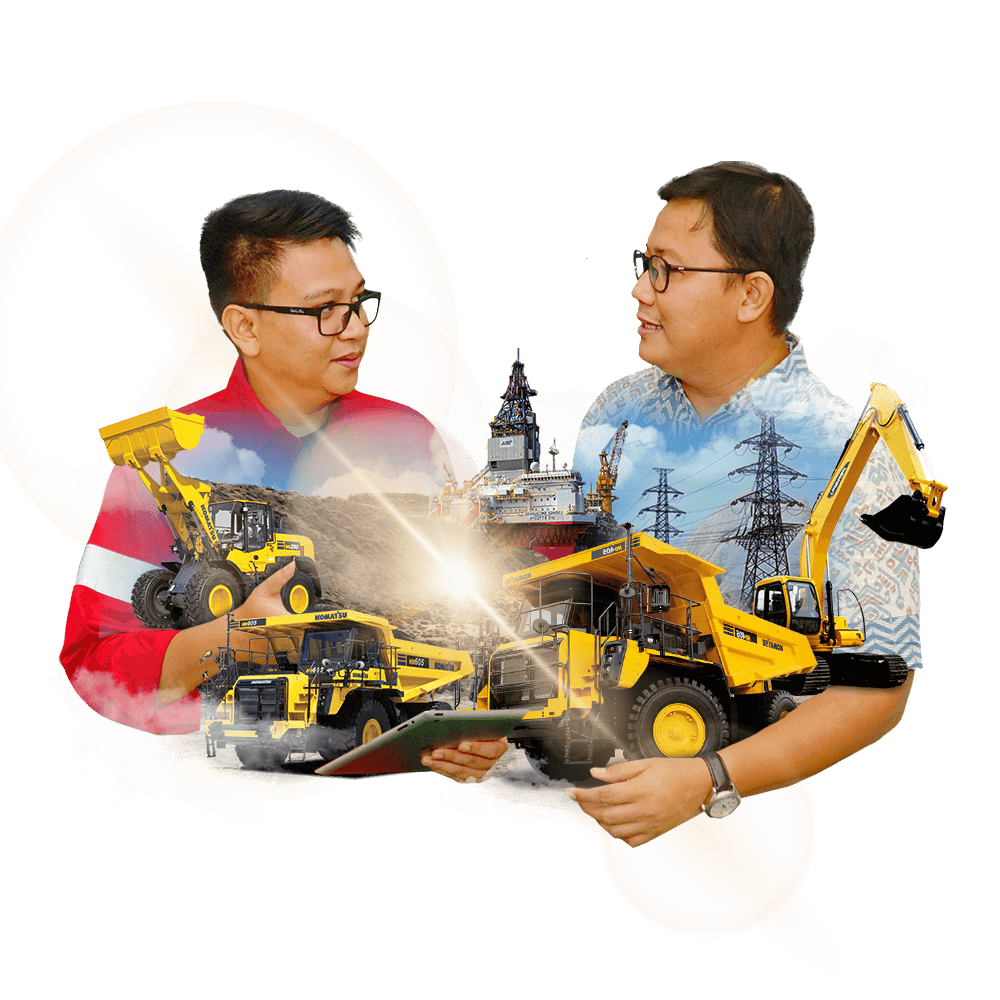