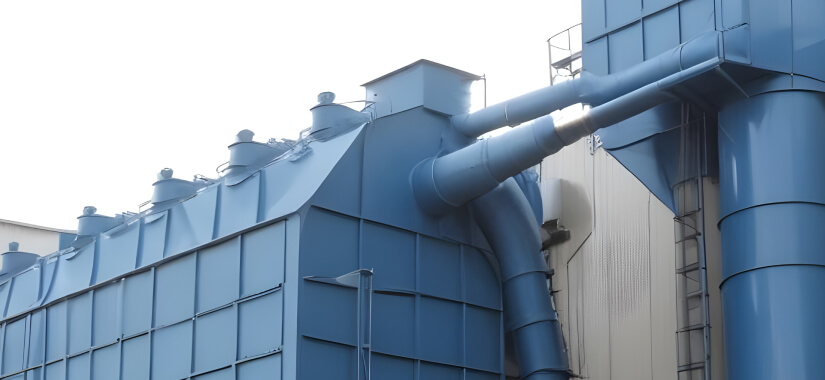
The clinkerization process in the cement industry is a crucial stage in cement production where raw materials such as limestone, clay, and other substances are heated in a kiln at very high temperatures, reaching approximately 1400 – 1450 degrees Celsius.
During this process, these materials undergo complex chemical reactions to produce clinker, which is a nodular material composed of calcium silicate. This clinker is then cooled and ground together with gypsum to produce cement.
Clinkerisation process problems and solutions:
1. Problem: High Temperature Grease
The issue of high-temperature grease in the clinkerization process in the cement industry arises due to the incorrect selection of grease. The grease used should be capable of operating at high temperatures.
Generally, high temperatures can cause grease to become more fluid, thereby reducing its ability to provide effective lubrication. This can lead to increased friction and wear on critical components.
Choosing the right grease is essential to maintain optimal machine performance and prevent potential damage and unwanted downtime.
Solution: Molykote / Dow / LE
The high-temperature grease we recommend as a solution includes: Molykote, Dow, and Lubrication Engineers (LE). These specialized grease products are designed to handle high temperatures optimally. Their formulas contain additives such as molybdenum disulfide (MoS2) or other additives that enhance the grease’s resistance to extreme temperatures, maintaining viscosity and lubrication stability during intensive operations.
Greases from Molykote, Dow, and LE are also designed to reduce friction and wear on heavy components such as bearings and gears, and provide additional protection against corrosion and oxidation.
Eonchemicals is the official distributor in Indonesia for Molykote, Dow, and Lubrication Engineers (LE) products. Through an official distributor, you will receive guarantees of product authenticity and quality assurance as per the original. Please contact us for more information.
2. Problem: Motor Cleaner for Gearbox
The issue of cleaning the motor on the gearbox in the clinkerization process in the cement industry involves the need to maintain cleanliness and optimal performance of the gearbox components involved in grinding raw materials such as limestone and clay.
Dust and fine particles from raw materials can accumulate around the gearbox, disrupting internal functions such as bearings and gears, which can lead to increased friction, faster wear, and even mechanical damage if not properly addressed.
Solution: EonMotor 100
This electric motor cleaner, made from a solvent blend, is designed to clean electric motors and dynamos from dust, oil, and grease, effectively removing contaminants.
When used correctly, this product helps keep electric motors clean and functioning well, thereby extending their service life and enhancing overall performance.
Regularly cleaning electric motors with the appropriate cleaner like EonMotor 100 is an important preventive maintenance step that can save repair and replacement costs in the future.
3. Problem: Road Dust
Scattered dust can cause various issues, including visibility disturbances, health risks for workers, and potential damage to equipment. Additionally, uncontrolled dust can spread to the surrounding environment, polluting the air and causing complaints from the local community.
Poor dust management can also lead to accumulation on road surfaces, worsening road conditions. Therefore, controlling road dust is crucial to maintaining safety, health, and efficiency.
Solution: DustDown 369, CSS
The appropriate solutions for the above issues are DustDown 369 and CSS. Both are designed to control and suppress dust in the cement industry. DustDown 369 works by binding dust particles together, increasing their size and weight, preventing them from becoming airborne.
CSS (Chemical Stabilizing Solution) works by stabilizing the road surface, reducing abrasion and dust formation caused by heavy vehicle movement and wind.
Please contact us to discuss solutions to your problems.
4. Problem: Grease Quality
The issue of grease quality in the clinkerization process in the cement industry relates to the challenge of ensuring that the grease used can withstand harsh and demanding operational conditions.
Grease that does not meet specifications can lead to inadequate lubrication, increased friction, and wear on critical components such as bearings and gears. This can result in equipment damage, downtime, reduced productivity, and increased operational costs at the cement plant.
Solution: Molykote / Dow / LE
Molykote, Dow, and Lubrication Engineers (LE) are the right grease lubricants to address the above issues. Their formulas are designed to withstand harsh, dusty, and high-temperature operational conditions.
All three are internationally recognized brands with proven performance. You will receive these products with guarantees of authenticity and quality assurance as per the original from Eonchemicals as the official distributor in Indonesia.
By using these high-quality greases, cement plants can ensure consistent and effective lubrication, improve operational efficiency, reduce downtime, and minimize maintenance costs.
5. Problem: Floors (Slippery and Damaged)
Slippery and damaged floors in the clinkerization process in the cement industry are commonly encountered issues. The impact of these problems includes worker safety and operational efficiency. Oil spills, chemicals, and heavy loads on the floor are the main causes. Incorrect selection of coating can be fatal, as it can reduce work efficiency and increase maintenance and operational costs.
Solution: EonCoat 551 / EonCoat 470
EonCoat 551 and EonCoat 470 are the right solutions for slippery and damaged floors, as both are protective coatings specifically designed to enhance safety and extend the life of the floor.
After curing, these products create a very hard layer with high resistance to impact, oil, and chemicals. They can be applied to new construction surfaces or used as a primer for anti-corrosion coating systems in buildings, offshore, petrochemical, mining, chemical industries, and others.
6. Problem: Water Treatment
Water treatment issues in the clinkerization process in the cement industry include challenges in managing the water used in various production processes, such as cooling and cleaning. The water used is often contaminated with fine particles from raw materials such as limestone and clay, as well as chemical residues.
This contamination can cause blockages in piping systems and equipment, reduce cooling efficiency, and increase the risk of scale and corrosion, leading to machine damage. If these problems are not properly addressed, they can disrupt smooth operations and escalate costs.
Solution: Coagulants and Flocculants
Eonchemicals provides solutions in the form of coagulants and flocculants to address water treatment issues in the clinkerization process as described above. Both function to gather and precipitate fine particles and contaminants in the water.
Coagulants work by binding small particles into larger ones. Flocculants are used to perfect the coagulant’s task, gathering these particles into larger flocs to make them easier to settle.
By using coagulants followed by flocculants, impurities in the water such as limestone and clay can be more effectively and efficiently precipitated. Subsequently, the clean water will be safer to use in piping systems and equipment, improving cooling efficiency and preventing scale, corrosion, and machine damage.
7. Problem: Boiler
Boiler issues in the clinkerization process in the cement industry include challenges in maintaining the optimal performance and operational reliability of boilers used to provide steam or heat in the production process. Common boiler problems include scale, corrosion, and fouling due to feedwater that is not properly treated or contaminated with fine particles from raw materials such as limestone and clay.
Scale and corrosion problems can reduce heat transfer efficiency, increase fuel consumption, and cause damage to boiler components. Fouling can also obstruct heat flow and reduce boiler efficiency.
Solution: Eon Boiler Chemicals
Eon Boiler Chemicals is an effective solution package for addressing boiler issues in the clinkerization process in the cement industry. These boiler chemical products are specifically designed to tackle scale, corrosion, and fouling problems. The Eon Boiler Chemicals solution package has formulations that condition boiler feedwater and prevent scale formation by binding scale-causing minerals so they remain dissolved in the water.
When used correctly, Eon Boiler Chemicals help maintain the optimal performance and operational reliability of boilers. Please consult with our team for details on boiler solution products, including dosing and application methods.
| Read grinding process problems and solutions on this site
8. Problem: Cooling Tower
Cooling tower issues in the clinkerization process in the cement industry involve challenges in maintaining optimal cooling efficiency during production. Cooling towers are used to dissipate heat generated during operations.
Common problems with cooling towers include scale, rust, and algae formation on tower surfaces, as well as mineral buildup and deposits from the water used for cooling. These issues can reduce heat transfer efficiency, increase water consumption, and affect the quality of water reused in the process.
Solution: Eon Cooling Tower Chemicals
Eon Cooling Tower Chemicals include: EonBac GEO 9910, EonLine AG 5770, and EonScale T 2511. These products are effective solutions for cooling tower issues in the cement industry. Their formulations are specifically designed to address various problems related to cooling efficiency and water quality.
They provide solutions to combat corrosion, scale, algae, and other disruptive problems. Please chat with our team on WhatsApp for more details, usage instructions, and dosing information.
| Read about quenching process problems and solutions
9. Problem: Metal Repair
Metal repair issues in the clinkerization process in the cement industry often arise due to the extreme conditions in the kiln and other equipment exposed to constant and repeated high temperatures. Equipment such as kilns, preheaters, and coolers experience significant wear and corrosion due to exposure to extreme temperatures and chemicals involved in the process.
Damage to these metal parts can disrupt cement production, increase maintenance costs and downtime for repairs, and threaten operational safety. Therefore, proper handling of metal repair issues is crucial to maintaining the sustainability and operational efficiency of kilns and related equipment in the cement industry.
Solution: Metbond 581
Metbond 581 is a high-performance ceramic component specifically developed to rebuild metal components damaged by erosion and corrosion. This product can be easily applied to corroded or damaged components without welding.
| Read about power plant problems and solutions
Metbond 581 is ideal for rebuilding various components such as pump bodies, impellers, propellers, grates, valves, tube sheets, water tanks, rudders, and heat exchangers. This solution product creates a layer with high abrasion and erosion resistance, optimal physical and mechanical strength.
Consult with EON Now
We are ready to listen and provide the right chemical solution for you. Consultation with our experts is free!
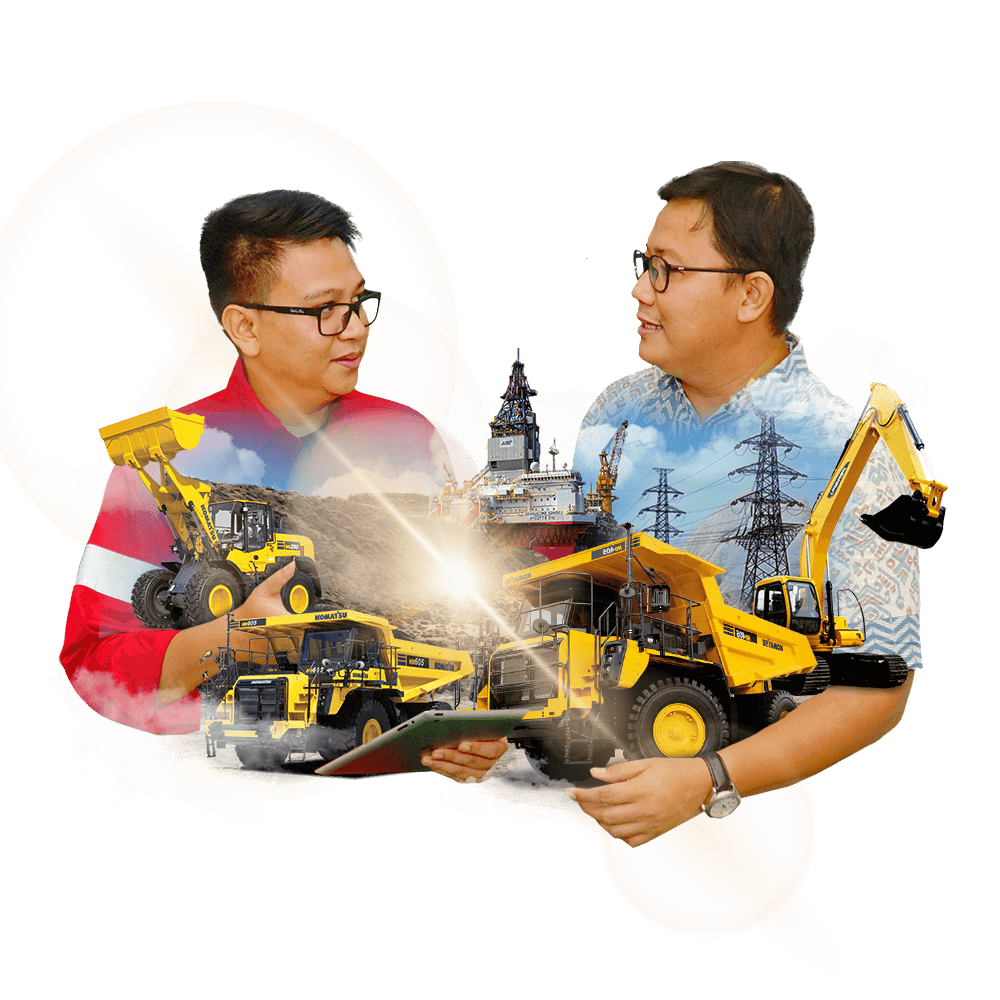