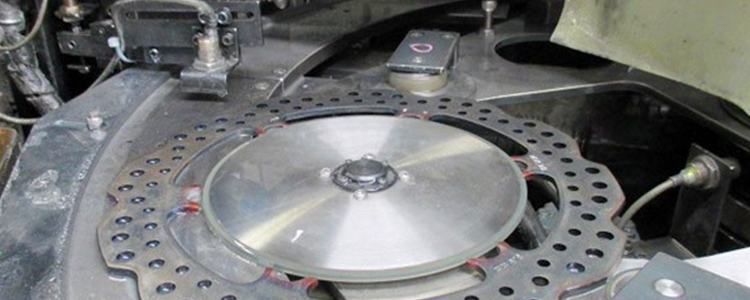
Grinding technology | Technology | YUTAKA
One of our customers encountered two significant issues: hardened sludge and frequent rust formation on the machine used in surface grinding applications for brake disc parts. These issues necessitated an increase in coolant concentration, leading to higher coolant consumption (inefficiency).
Sludge, or slurry waste, is a byproduct of the grinding process and can become a serious problem if not properly managed.
The problems that may arise include:
- Causing rust
- Emitting foul odors
- Clogging circulation pathways
- Rejecting parts
- Tank leakage
Field observations with the customer revealed the following facts:
- Hardened sludge occurs in all machines
- Rust is present in all machines
- The coolant used is of the synthetic type
- High concentration is used to prevent rust
It can be concluded that the hardened sludge and rust on the machines are due to the clinkering/hot chip process, which causes rapid hardening. This hardening and the subsequent difficulty in cleaning result in accumulation in the tank, thereby reducing the rust protection capability of the coolant.
Solution
We recommend trialing EONTRIM SC310, a semi-synthetic microemulsion coolant, for surface grinding applications.
Features and Benefits of EONTRIM SC310:
- Specifically formulated to prevent hot chips and clinkering commonly encountered in machining cast iron
- Contains anti-rust agents that form an easily cleanable film on the machine
- Includes EP additives for a good surface finish and extended tool life
Results
After a one-month trial, the following results were obtained:
Parameter | Existing | EONTRIM SC310 |
Coolant type | Synthetic | Microemulsion |
Range concentration | 5-7% | 3-5% |
Consumption/machine/month | 90 L | 60 L |
Toishi tool life (pcs/tool) | 900,000 | 1,400,000 |
Cost coolant/piece (IDR) | 235 | 164 |
Cost-saving: | ||
a. Consumption | 33% | |
b. Tool life | 56% | |
c. Cost coolant/piece | 30% |
Conclusion
The initial goal of the trial was to eliminate hardened sludge, which was successfully achieved. Additionally, the customer experienced further improvements, such as:
- No occurrence of hardened sludge
- Coolant consumption reduced by 33%
- Tool life of Toishi increased by 56%
- Coolant cost per piece saved by 30%
By selecting the appropriate coolant, the customer can save time, materials, and costs.
For free consultation regarding machining problems, please contact us.
Consult with EON Now
We are ready to listen and provide the right chemical solution for you. Consultation with our experts is free!
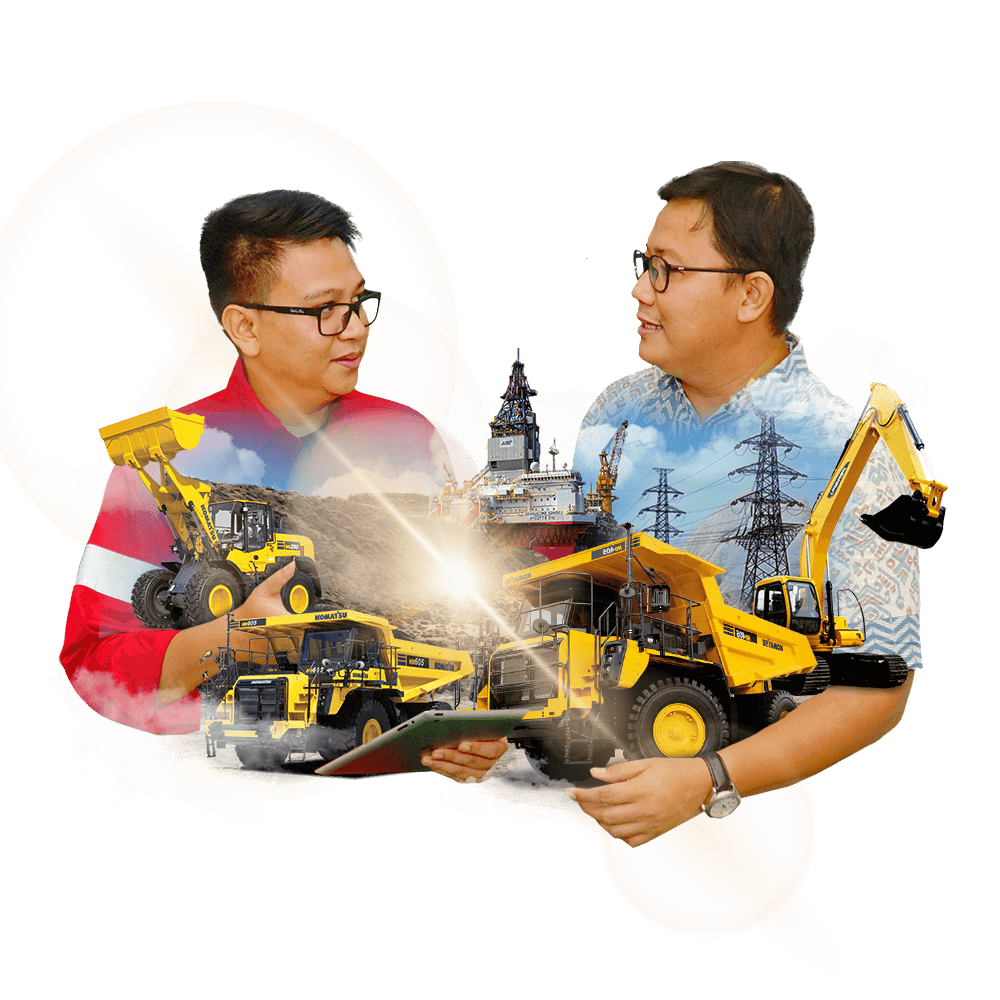